Die Entscheidung, ob ein eigener CNC-Maschinenpark aufgebaut werden soll oder ob die Dienste eines Zulieferers in Anspruch genommen werden sollen, der auf Bestellung mechanische Komponenten herstellt, gehört zu den wichtigsten operativen Entscheidungen in der Industrie. Diese Entscheidung wirkt sich nicht nur auf die Finanzen des Unternehmens aus, sondern auch auf die Zeit bis zur Einführung neuer Produkte, die Verfügbarkeit von Technologien, die operative Flexibilität und das Projektrisiko.
Nicht jedes produzierende Unternehmen muss Millionen in moderne Bearbeitungszentren investieren und seine technologische Infrastruktur von Grund auf aufbauen. Andererseits lohnt es sich nicht immer, Prozesse, die für Qualität, Vertraulichkeit und Präzision entscheidend sind, an externe Dienstleister auszulagern.
In diesem Artikel analysieren wir beide Ansätze. Die Investition in Maschinen und das Outsourcing der CNC-Bearbeitung, basierend auf konkreten Zahlen, realistischen Szenarien und bewährten Marktpraktiken.
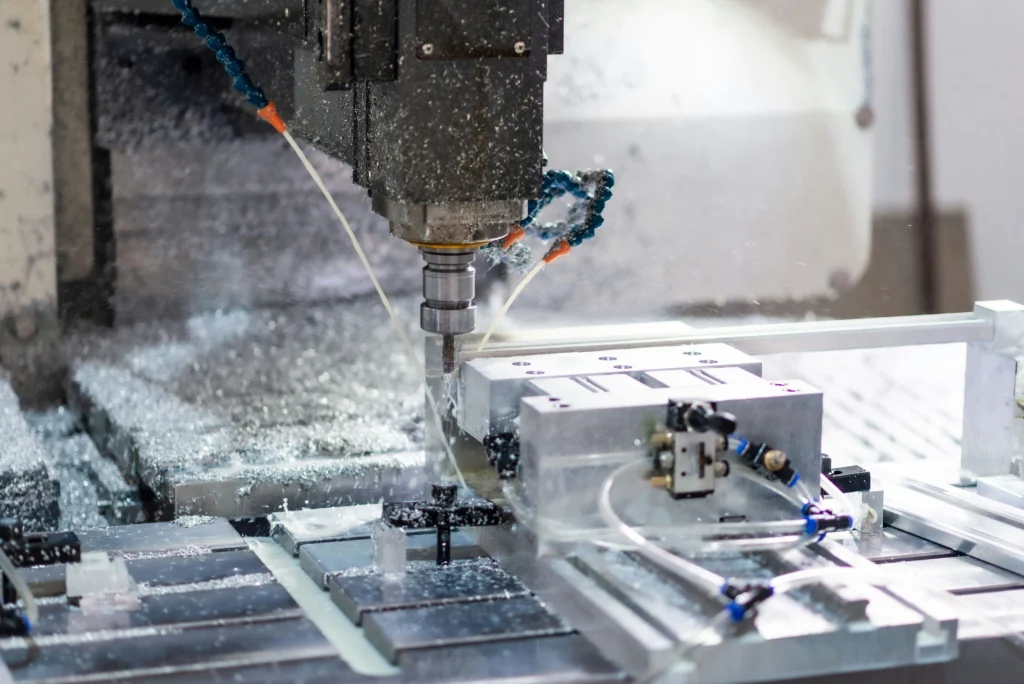
Investitionskosten für einen CNC-Maschinenpark–was muss wirklich berücksichtigt werden?
Der Kauf einer Maschine ist nur der Anfang. Ein eigener CNC-Maschinenpark verursacht eine Reihe von zusätzlichen Kosten, die bereits in der Investitionsplanungsphase berücksichtigt werden müssen:
- Kauf einer Maschine: 3-Achsen-VMC-Fräsmaschinen – von 250 bis 650 Tausend PLN; 5-Achsen-Zentren – von 1 bis sogar 2,5 Millionen PLN.
- CAD/CAM-Software: 60.000 bis 150.000 PLN, je nach Komplexität der Bearbeitung und Hersteller.
Es ist zu beachten, dass CAM-Systeme als unbefristete Lizenzen mit einer jährlichen Gebühr für Updates oder im Abonnementmodell angeboten werden können, bei dem die Kosten jährlich anfallen. Die Preisunterschiede ergeben sich aus dem Funktionsumfang, der Anzahl der Achsen der Werkzeugmaschine, dem Zugang zu Simulationen und Postprozessoren.
- Werkzeugausstattung: Schraubstöcke, Sonden, Halterungen, Werkzeuge – in der Regel ca. 20 % des Maschinenwertes.
- Anpassung der Halle: geeignete Fundamente, Kühlung, Stromversorgung – weitere 10–15 % der Investition.
- Wartung und Inspektionen: durchschnittlich 5–7 % des Maschinenwertes pro Jahr.
- Technisches Personal: CNC-Bediener, CAM-Programmierer – unverzichtbar für die tägliche Arbeit.
Für ein Beispielzentrum mit 5 Achsen können die jährlichen Betriebskosten – ohne Berücksichtigung der Abschreibung – leicht 400.000 PLN übersteigen. Dies ist eine echte Herausforderung, insbesondere wenn die Maschine nicht unter Volllast arbeitet.
Quelle: want.net – CNC Machine Cost Explained
Sind 2000 Stunden die Rentabilitätsschwelle?
In der Industrie geht man davon aus, dass etwa 2.000 Betriebsstunden pro Jahr die ungefähre Rentabilitätsschwelle für die Investition in eine CNC-Werkzeugmaschine darstellen. Woher kommt diese Zahl? Das entspricht in etwa der Vollauslastung einer Maschine im Einschichtbetrieb: 8 Stunden pro Tag, 5 Tage pro Woche, 50 Wochen pro Jahr (mit einer Reserve für Wartungsausfälle und Feiertage).
Oberhalb dieser Grenze beginnt sich die Investition zu amortisieren – die Stückkosten sinken und die Kapitaleffizienz steigt. Je länger die Maschine läuft, desto besser ist der ROI (Return on Investment).
In der Praxis ist diese Schwelle jedoch schwer zu erreichen. Marktdaten zeigen, dass die durchschnittliche Auslastung von CNC-Maschinen in Ein-Schicht-Betrieben nur 26 % der verfügbaren Produktionszeit beträgt – also deutlich weniger als die erforderlichen 2.000 Stunden. Dies ist auf unvollständige Auslastung, Ausfallzeiten, Umrüstungen und schwankende Aufträge zurückzuführen.
Fazit? 2.000 Stunden sind ein realistisches, aber ehrgeiziges Ziel, das sich nur bei einem regelmäßigen, gut geplanten Produktionsvolumen lohnt. In allen anderen Fällen sollte Outsourcing als Lösung mit geringerem finanziellen Risiko in Betracht gezogen werden.
Quelle: https://www.machinemetrics.com/stateoftheindustry2022
Wann lohnt sich eine eigene CNC-Maschinenflotte?
Eine eigene CNC-Maschinenflotte ist eine Lösung, die konkrete Vorteile bringen kann. Vor allem dann, wenn:
- Sie in Serie und in großem Umfang produzieren – und eine konstante, intensive Auslastung Ihrer Maschinenflotte gewährleisten können. Dann sinken die Stückkosten deutlich.
- Sie benötigen sehr schnelle Prototypenentwicklung und häufige technologische Änderungen – zwar bieten einige erfahrene Zulieferer solche Unterstützung an, aber eigene Maschinen vor Ort verkürzen die Reaktionszeiten und ermöglichen eine flexiblere Entscheidungsfindung.
- Sie legen Wert auf den Schutz Ihres technologischen Know-hows – insbesondere in Branchen wie der Luftfahrt, der Medizin oder der Verteidigungsindustrie. Obwohl professionelle Auftragnehmer Vertraulichkeitsvereinbarungen (NDAs) unterzeichnen, ziehen es einige Unternehmen vor, sensible Daten und Prozesse ausschließlich innerhalb der Organisation zu halten.
- Sie möchten die volle Kontrolle über den Bearbeitungsprozess – nicht nur in Bezug auf die Qualität, sondern auch hinsichtlich der Optimierung der Arbeitsabläufe, der Instandhaltung und der Integration in Ihre eigenen Kontrollsysteme.
Obwohl einige dieser Anforderungen von externen Auftragnehmern erfüllt werden können, bietet der Besitz eigener Maschinen dem Unternehmen Entscheidungsfreiheit, kürzere Reaktionszeiten und das Potenzial zur Optimierung der Technologie in Echtzeit.
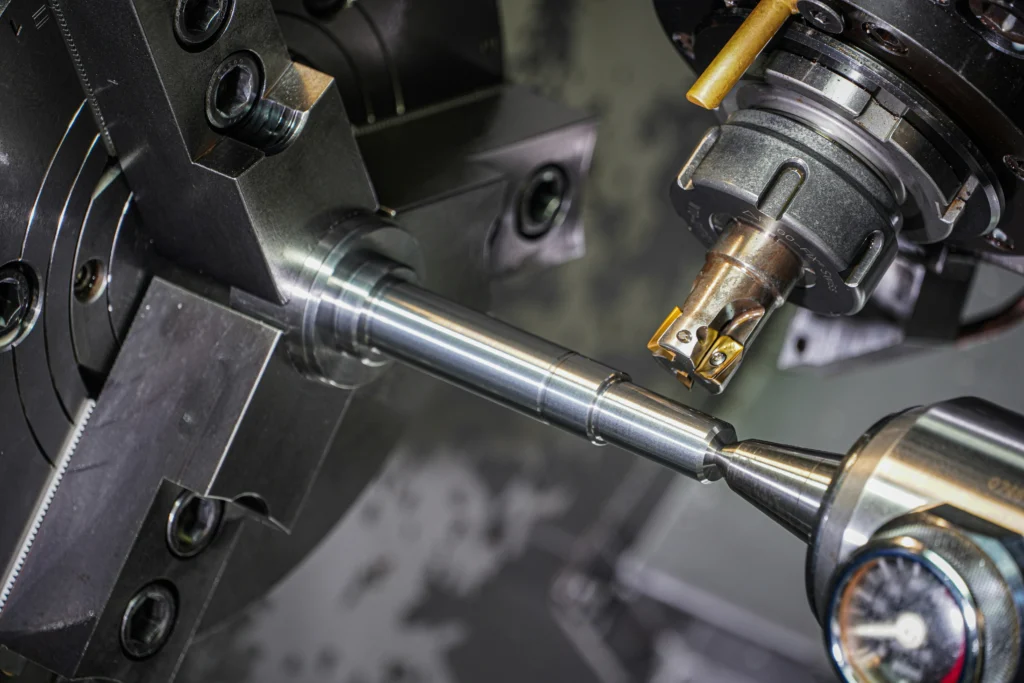
Was bietet das Outsourcing der CNC-Bearbeitung?
Das Outsourcing der Fertigung mechanischer Komponenten ist heute weit mehr als nur die Vergabe eines Auftrags zur Herstellung eines Teils. Moderne Dienstleistungsunternehmen werden zu Technologiepartnern und bieten Zugang zu Spezialmaschinen, ohne dass eine eigene Infrastruktur von Grund auf aufgebaut werden muss.
Im Rahmen einer einzigen Zusammenarbeit erhalten Sie:
- Viele Technologien aus einer Hand – 5-Achs-Fräsen, Drehen, Elektroerosion (EDM), Eloxieren, Härten, Entgraten und vieles mehr.
- Technische Unterstützung – Optimierung der Konstruktion im Hinblick auf eine einfache und wirtschaftliche Fertigung (DFM – Design for Manufacturing). Dabei wird das Design eines Bauteils so angepasst, dass seine Herstellung vereinfacht, die Anzahl der Arbeitsschritte reduziert, schwer einzuhaltende Toleranzen vermieden und die Materialauswahl optimiert werden.
- Systematische Qualitätskontrolle – umfasst unter anderem präzise Messungen von Details mit Koordinatenmessgeräten (CMM – Coordinate Measuring Machine), mit denen die Maßhaltigkeit anhand der technischen Dokumentation genau überprüft werden kann. Hinzu kommt die vollständige Rückverfolgbarkeit des Produktionsprozesses (sog. Traceability), d. h. die Möglichkeit, nachzuvollziehen, aus welchen Materialien und unter welchen Bedingungen jedes Element hergestellt wurde. Im Rahmen der Kontrolle können auch Konformitätszertifikate und Ergebnisse der Endprüfungen geliefert werden.
- Modell ohne Fixkosten – keine Investitionen in Maschinen, kein Service, keine Ausfallzeiten. Sie bezahlen nur für die tatsächlich geleistete Arbeit.
Wichtig ist auch, dass Outsourcing auch den Zugang zum Erfahrungsschatz eines Teams bedeutet, das seit Jahren Projekte für viele Branchen realisiert. Diese Erfahrung führt zu einer besseren technologischen Beratung, schnelleren Implementierungen und einem geringeren Fehlerrisiko in der Produktionsphase.
Wann hat das Outsourcing der CNC-Bearbeitung Vorteile?
Outsourcing der CNC-Bearbeitung ist eine Überlegung wert, wenn:
- die Maschinenauslastung 2000 Stunden pro Jahr nicht überschreitet,
- die Projekte variabel, unregelmäßig oder saisonabhängig sind,
- Sie keine personellen Ressourcen haben,
- Sie keine Kosten für Service, Wartung und Ausfallzeiten tragen möchten,
- Sie Zugang zu vielen Technologien ohne Kapitalinvestitionen benötigen.
Immer mehr Unternehmen nutzen ein gemischtes Modell, bei dem die Kernproduktion im eigenen Haus verbleibt und komplexere oder gelegentliche Aufträge an externe Partner vergeben werden.
Zusammenfassung
Die Entscheidung, ob Sie einen eigenen Maschinenpark aufbauen oder die CNC-Bearbeitung auslagern sollten, hängt nicht nur von den Stückkosten ab. Es handelt sich um eine strategische Entscheidung, die sich auf das Betriebsmodell, die Kostenstruktur und die Geschwindigkeit der Projektabwicklung auswirkt.
Investitionen in Maschinen lohnen sich, wenn ein großes, stabiles Volumen, die Notwendigkeit einer vollständigen Prozesskontrolle und klar definierte technische Kompetenzen innerhalb des Unternehmens vorhanden sind. Dieses Modell bietet Unabhängigkeit, erfordert jedoch Kapital, Planung und eine hohe Maschinenauslastung, um rentabel zu sein.
Die Auslagerung der CNC-Bearbeitung ist hingegen eine flexible, skalierbare und finanziell risikoarme Lösung. Sie eignet sich gut für Unternehmen, die mit schwankender Nachfrage zu tun haben, neue Produkte entwickeln oder schnellen Zugang zu Technologien benötigen, deren dauerhafte Einführung sich nicht lohnt.