Aluminum is a material widely used in the production of mechanical components. Its light weight, corrosion resistance, and favorable strength-to-weight ratio make it ideal for precision engineering applications. But what makes aluminum such an attractive material also means that its machining requires more than just a standard approach.
CNC machining is now the basis of modern production, including when working with aluminum. However, the effectiveness of the entire process depends on many factors. From the selection of tools and coatings, through cutting parameters, to the cooling method. It is these elements that determine the surface quality, repeatability, and durability of the finished part.
Drawing on our many years of experience in CNC metalworking, this article describes specific solutions that have proven themselves in production and allow you to achieve stable quality of the finished part.
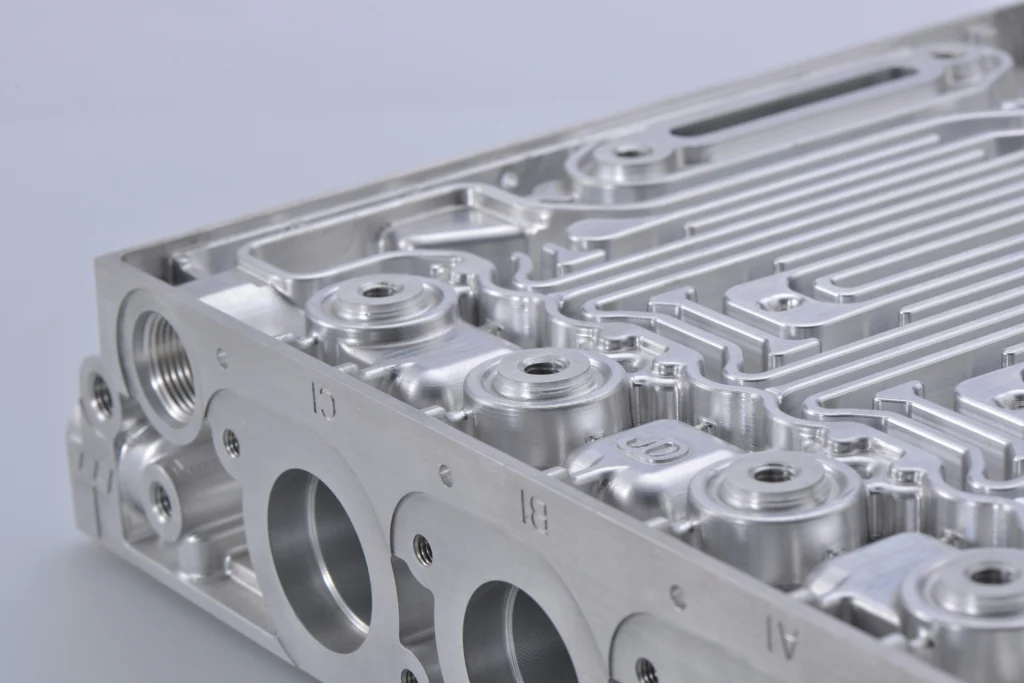
Aluminum – material specifications and problems encountered in CNC machining
Before we move on to cutting strategies, it is worth taking a look at the properties of aluminum that directly influence the choice of machining parameters. Understanding these properties is crucial for the stability and repeatability of the entire process.
Materialproperties | What does this mean in practice? |
Low density (2.6–2.8 g/cm³) | Aluminum is lightweight, which allows for higher rotational speeds and feed rates, and the machine is not as heavily loaded as with steel. |
High thermal conductivity | Heat quickly escapes from the cutting zone, but mainly to the tool. Without efficient cooling, the blades overheat and wear out faster. |
Low hardness (HV ≈ 25–120) | Sharp tools with a large rake angle can be used. Cutting is smooth and the load on the machine tool remains low. |
Viscosity and adhesion | Aluminum tends to stick to the blade. Friction-reducing coatings, polished chip grooves, and properly selected cooling help to prevent this. |
Although at first glance, turning and milling aluminum seems “easy,” in practice it requires a great deal of attention and technological precision.
Aluminum alloys and their machinability with CNC technology
Not all aluminum behaves the same when in contact with a tool. Depending on the chemical composition and hardness, different alloys may require completely different cutting parameters—from speed and force to optimal spindle speed, control, and cutting tool.
Below are a few examples of popular alloys used in the production of aluminum components:
- EN AW-1050A (1xxx series) – pure aluminum, very soft, malleable, the main disadvantage is the low strength of the alloy.
- EN AW-5083 (5xxx series) – contains magnesium, corrosion resistant, used in the marine industry. Requires greater cutting force.
- EN AW-6082 (6xxx series) – universal alloy, responds well to various cutting strategies, popular in machine construction.
- EN AW-7075 (7xxx series) – a very hard alloy with zinc and magnesium, used in aviation. More difficult to machine, requires sharp and very durable tools.
Knowledge of the type of aluminum alloy facilitates the machining of the material. Without it, it is difficult to select the right tools, set the cutting parameters, and predict the behavior of the workpiece during production.
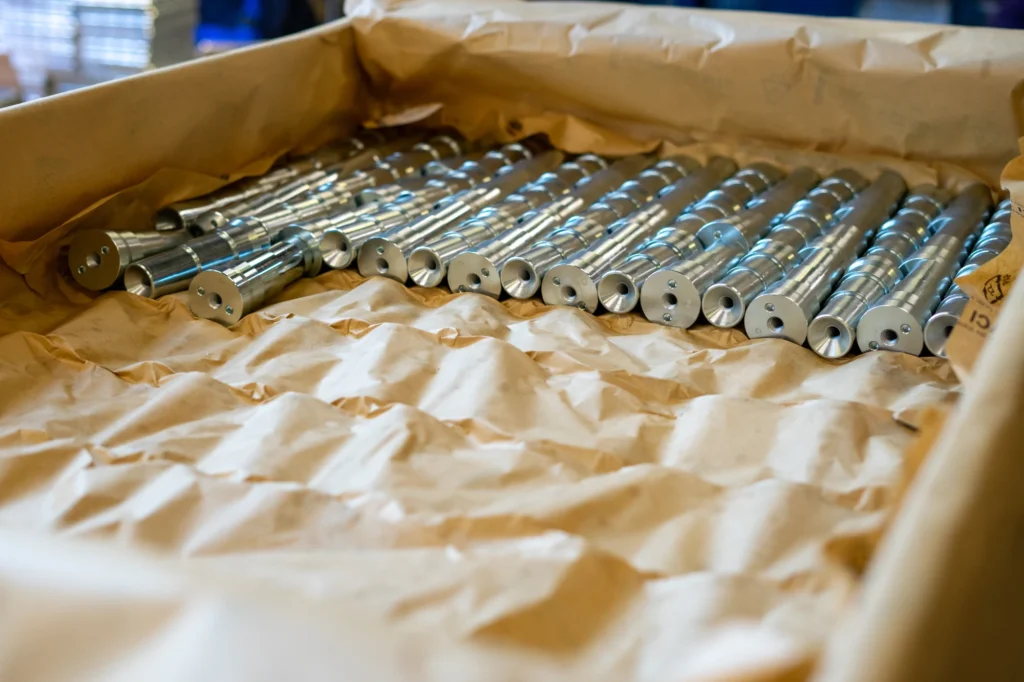
Main processes and types of CNC aluminum machining
Aluminum can be effectively machined in several different ways, depending on the needs of the project and the expected results.
CNC milling
It works well for both precision components and large structural blocks. Concurrent milling gives a better surface quality, while counter-rotating milling is suitable where stability is required.
For larger volumes of material, full milling is used. Thin-walled parts are machined with minimal allowance and well-chosen cooling.
CNC turning
Used for axially symmetrical parts: shafts, sleeves, rings.
In turning, it is crucial to maintain a stable feed rate and the correct cutting edge radius, especially for thin-walled parts.
If the cutting parameters are too low, vibrations and an irregular surface will occur. If they are too aggressive, excessive chip accumulation and the risk of workpiece deformation will occur.
Drilling and threading
The most common problems are burrs and hole deformation. Drills with a larger point angle and good chip removal are used. Forming taps are suitable for threading — they do not cut, but shape the thread.
This eliminates chips and strengthens the connection, especially in thin-walled components.
Grinding and surface preparation
Surface quality is crucial for anodizing. Any scratches will be visible after oxidation.
Therefore, parts are often subjected to additional finishing operations — finishing milling or grinding with emulsions and fine-grained abrasives.
CNC tools used for machining aluminum
For aluminum, it is essential to use tools that enable efficient chip removal and reduce the risk of material build-up on the cutting edge.
The most commonly used types of tools are:
- Single- and double-edged end mills – their large chip flutes and positive rake angle promote smooth cutting and effective chip removal. They are particularly suitable for milling pockets and contours.
- Spiral drills – with sharp geometry and an aggressive rake angle. They allow for fast drilling without clogging the holes, even at greater depths.
- Turning tools with positive insert geometry – used for turning aluminum parts. This geometry reduces cutting force and the risk of build-up.
- PCD-tipped milling cutters and drills – used in series production. Thanks to diamond tips brazed onto a carbide body, they ensure the highest quality finish, especially on thin-walled components.
The choice of tool depends on the technological operation, workpiece geometry, and quality requirements. Each tool has its own specific characteristics and is best suited for specific applications.
Cooling and lubrication of aluminum during the machining process
CNC machining of aluminum requires special attention in terms of cooling, as aluminum quickly transfers heat to the tools. Lack of effective cooling quickly leads to a deterioration in the surface quality of the parts, accelerates tool wear, and can also cause thermal deformation of the workpiece.
The most commonly used cooling and lubrication methods are:
- Flood (flood cooling) – involves intensive cooling of the machining area with a large amount of cooling emulsion. This method is effective for machining larger aluminum components.
- MQL (Minimum Quantity Lubrication) – cooling with a minimum amount of lubricant, supplied in the form of an oil mist. This solution is particularly useful when preparing aluminum parts for the aluminum anodizing process, when the cleanliness of the workpiece surface is important.
- Air cooling with wax additive – mainly used in prototyping and less intensive machining. This method reduces the amount of coolants and is economical, but does not work well in demanding production processes.
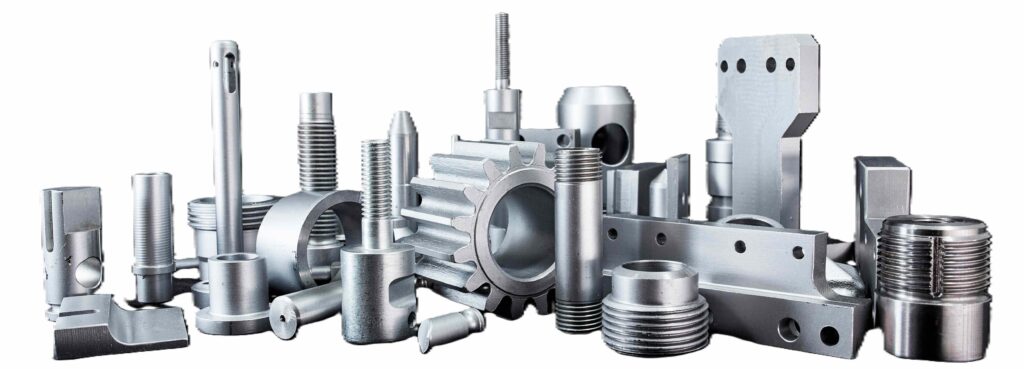
Modern aluminum cutting strategies
One of the most popular approaches is HPC (High Performance Cutting) – a deep cutting technique with a narrow blade width. It allows for a significant increase in feed rate without the risk of tool overload or deterioration of workpiece parameters.
HSC (High Speed Cutting) is ideal for thin-walled aluminum components. Thanks to very high rotational speeds and low cutting forces, this method ensures precise milling without deformation, even of delicate structures.
Trochoidal milling is also becoming increasingly popular – a strategy that involves guiding the tool along a curved, dynamic path. This ensures even blade wear, better cooling, and minimizes mechanical and thermal loads.
Summary – aluminum rewards precision
Aluminum is a material with great potential, but also with complex technological characteristics. To achieve repeatable quality and high performance in CNC machining, a good machine is not enough. You need well-chosen tools, well-thought-out cutting strategies, effective cooling, and knowledge of the properties of the specific alloy.
It is precisely this approach — based on practice and experience — that allows you to fully exploit the potential of aluminum and avoid typical production problems.