CNC-Bearbeitung von Kunststoffen–Herausforderungen und Materialspezifika
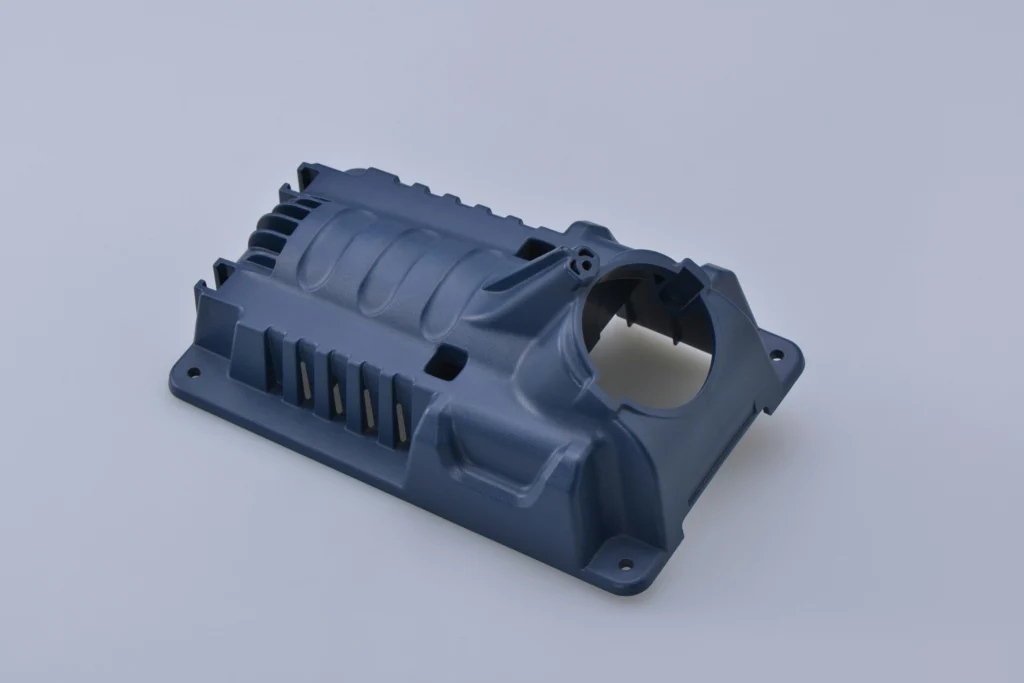
In den letzten Jahrzehnten haben sich Kunststoffe in vielen Branchen – von der Automobilindustrie über die Elektronik bis hin zur Medizin und vielen anderen – zu einem vollwertigen Konstruktionsmaterial entwickelt. Ihre wachsende Beliebtheit ist auf eine Kombination aus geringem Gewicht, chemischer Beständigkeit und einer Vielzahl mechanischer Eigenschaften zurückzuführen, die an die jeweilige Anwendung angepasst werden können. Gleichzeitig unterscheidet sich die CNC-Bearbeitung von Kunststoffen erheblich vom Zerspanen von Metallen. Polymere verhalten sich unter dem Einfluss von Wärme, Feuchtigkeit und inneren Spannungen völlig anders. Dies erfordert einen anderen Ansatz bei der Konstruktion, der Auswahl der Werkzeuge und den Fertigungsstrategien. In diesem Artikel werden wir uns mit den Besonderheiten der CNC-Bearbeitung von Kunststoffen befassen – wir werden die häufigsten technologischen Herausforderungen, die Unterschiede im Ansatz im Vergleich zu Metallen und die entscheidenden Faktoren für die Qualität und Wiederholbarkeit der Produktion diskutieren. Warum unterscheidet sich die CNC-Bearbeitung von Kunststoffen von der von Metallen? Kunststoffe verhalten sich im Bearbeitungsprozess anders als Metalle, was hauptsächlich auf ihre physikalischen und strukturellen Eigenschaften zurückzuführen ist. Drei Faktoren spielen dabei die größte Rolle: Zusammenfassend lässt sich sagen, dass bei Polymeren die Kontrolle der Temperatur, die Berücksichtigung innerer Spannungen und die feuchtigkeitsbedingte Dimensionsstabilität von entscheidender Bedeutung sind. Eigenschaften ausgewählter Materialien bei der CNC-Bearbeitung von Kunststoffen Aufgrund der Vielfalt der Kunststoffe lässt sich kaum von einer universellen Bearbeitungsmethode sprechen. Jedes Polymer verhält sich unter dem Einfluss von Temperatur, Feuchtigkeit oder mechanischer Belastung anders. POM (Acetal) – das am besten vorhersehbare technische Polymer POM gilt als der am einfachsten zu bearbeitende Konstruktionswerkstoff. Er zeichnet sich durch geringe Feuchtigkeitsaufnahme, Dimensionsstabilität und gute Oberflächenqualität nach dem Zerspanen aus. Daher ist er oft die erste Wahl bei der Herstellung von Präzisionsmechanikteilen, die eine hohe Maßhaltigkeit erfordern. PA (Nylon) – ein Material, das einer Feuchtigkeitskontrolle bedarf Nylon zeichnet sich durch eine hohe mechanische Festigkeit aus, hat jedoch den Nachteil einer starken Hygroskopizität. Das aufgenommene Wasser verändert nicht nur die Abmessungen, sondern auch die Härte und Elastizität des Materials. Aus diesem Grund trocknen viele Betriebe die Halbzeuge vor der Bearbeitung und führen vor dem Zerspanen eine Spannungsarmglühung durch. (Wärmebehandlung, bei der das Material erhitzt, auf einer bestimmten Temperatur gehalten und langsam abgekühlt wird, um innere Spannungen zu beseitigen) PC (Polycarbonat) – stark, aber anfällig für Spannungsrisse Polycarbonat wird wegen seiner außergewöhnlichen Schlagfestigkeit geschätzt. Leider neigt es gleichzeitig zu Mikrorissen unter dem Einfluss innerer Spannungen und bei Kontakt mit bestimmten Kühlmitteln und Lösungsmitteln. Um das Risiko zu verringern, werden scharfe Werkzeuge, eine Kühlung mit neutralen Medien und ein Glühprozess bei kritischen Bauteilen eingesetzt. PMMA (Acryl) – Kunstst off für optische Anwendungen Acryl ist ein beliebtes Material, wenn Transparenz und eine hohe Ästhetik der Oberfläche gefordert sind. Um jedoch Dimensionsstabilität zu erreichen, ist sowohl vor als auch nach der Bearbeitung ein Ausglühen erforderlich. In optischen Anwendungen wird zusätzlich eine Flamm- oder chemische Politur angewendet, um Mikrorisse zu entfernen und die Transparenz zu verbessern. PTFE (Teflon) – Problem mit der Fließfähigkeit des Materials PTFE ist ein Polymer mit einem sehr niedrigen Reibungskoeffizienten und einer ausgezeichneten chemischen Beständigkeit. Sein Nachteil ist seine Weichheit und seine Neigung zum sogenannten Kriechen – d. h. zur langsamen Verformung unter Belastung. Die CNC-Bearbeitung erfordert hier besonders starre Spannvorrichtungen und scharfe Werkzeuggeometrien. PEEK–Hochleistungspolymer PEEK ist eines der teuersten und fortschrittlichsten Konstruktionspolymere. Es zeichnet sich durch eine hohe thermische und mechanische Beständigkeit aus. Seine CNC-Bearbeitung ist relativ vorhersehbar, vorausgesetzt, das Material wurde zuvor einem Glühprozess unterzogen. Für glas- oder kohlefaserverstärkte Verbundwerkstoffe werden PCD- oder Diamantwerkzeuge empfohlen. Dimensionsstabilität und Toleranzen bei der CNC-Bearbeitung von Kunststoffen Eines der wichtigsten Themen bei der CNC-Bearbeitung von Kunststoffen ist die Dimensionsstabilität der Werkstücke. Diese hängt nicht nur von der Genauigkeit der Werkzeugmaschine ab, sondern auch von der Geschichte des Materials. Nach unserer Erfahrung ist es unter günstigen Bedingungen möglich, Toleranzen in der Größenordnung von ±0,0005 Zoll zu erreichen, jedoch nur bei stabilen Materialien (z. B. POM, PEEK) und bei entsprechender Kontrolle der Umgebungsbedingungen., but only for stable materials (e.g., POM, PEEK) and with proper environmental control. Die Bedeutung des Designs für Kunststoffe Das Design von Kunststoffteilen erfordert einen anderen Ansatz als bei Metallen. Polymere sind anfälliger für Spannungskonzentrationen, Verformungen oder das Schließen von Öffnungen nach der Bearbeitung. Daher müssen die Eigenschaften des Materials bereits in der Konstruktionsphase berücksichtigt werden. In der Praxis bedeutet dies unter anderem, dass scharfe Innenkanten (die Risse verursachen) vermieden, Radien in Ecken verwendet, geeignete Wandstärken gewählt und Gewindeeinsätze anstelle von direkt in den Kunststoff eingearbeiteten Gewinden bevorzugt werden sollten. Zusammenfassung Die CNC-Bearbeitung von Kunststoffen ist ein Bereich, der Erfahrung und Verständnis für die Besonderheiten des Materials erfordert. Im Gegensatz zu Metallen, bei denen Wärme und Spannungen leichter zu kontrollieren sind, erfordern Polymere eine individuelle Herangehensweise. Dank der Kenntnis dieser Zusammenhänge ist es möglich, eine hohe Oberflächenqualität und stabile Abmessungen zu erzielen, was Kunststoffe zu einem vollwertigen Material in der modernen Industrie macht.
CNC-Bearbeitung von Messing – Eigenschaften, Sorten und bewährte Verfahren
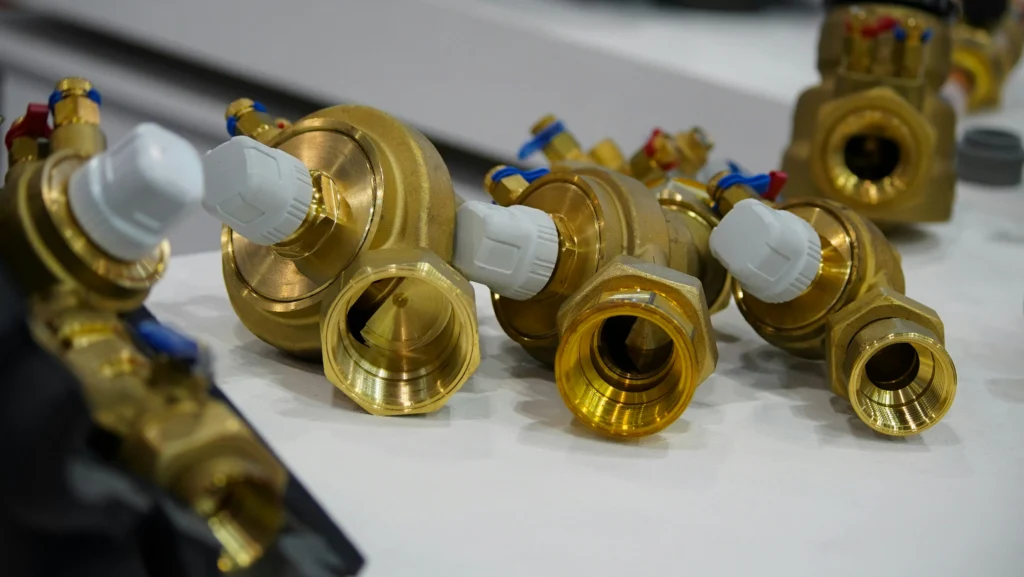
Brass, an alloy of copper and zinc, is one of the most commonly chosen nonferrous metals in CNC machining. It is valued for its ease of machining, corrosion resistance and attractive surface appearance. Thanks to these properties, it is used in fittings, electrical parts, precision components or decorative details. The importance of brass in industrial production is due not only to its functional properties, but also to the economy of the process – in many cases, it makes it possible to achieve high quality parts with relatively short processing times. In this article, we will introduce the properties of brass relevant to CNC machining, discuss the most common grades of this alloy, and suggest, based on our more than 45 years of experience, how to approach turning, milling, drilling or tapping for optimal results. Messing und CNC-Bearbeitung Bei der CNC-Bearbeitung von Metallen hebt sich Messing von vielen anderen Werkstoffen ab. Seine Wärmeleitfähigkeit verringert das Risiko einer Überhitzung der Werkzeuge, und seine relativ geringe Härte sorgt für einen reibungslosen Prozess. Dadurch sind hohe Schnittgeschwindigkeiten möglich und es lassen sich sehr glatte Oberflächen ohne zusätzliches Polieren erzielen. Es sind diese Eigenschaften, die das CNC-Drehen und -Fräsen von Messing zu einem besonders kostengünstigen Verfahren machen. Durch entsprechend ausgewählte Schnittparameter kann überschüssiges Material schnell abgetragen werden, während eine hohe Oberflächenqualität erhalten bleibt. Die gängigsten Messingqualitäten In der industriellen Praxis kommen mehrere wichtige Messingsorten zum Einsatz: Die Kenntnis dieser Unterschiede kann Ihnen helfen, Fehler zu vermeiden und Ihren Schneidprozess zu optimieren. CNC-Drehen und -Fräsen von Messing – was ist wissenswert? Das Drehen von Messing ist einer der grundlegenden Arbeitsschritte bei der CNC-Bearbeitung dieser Legierung. Damit der Prozess stabil ist und eine hohe Oberflächenqualität erzielt wird, werden folgende Werkzeuge verwendet: Auch das Fräsen von Messing ist ein sehr effizienter Prozess, vorausgesetzt, es werden die richtigen Werkzeuge ausgewählt: Bohren und Gewindeschneiden in Messing Das Bohren in Messing birgt eine besondere Schwierigkeit: Bei einigen Sorten, insbesondere bei weichen und duktilen, tritt ein Phänomen auf, das umgangssprachlich als „Bohrrückzug“ bezeichnet wird. Das bedeutet, dass das Werkzeug statt eines stabilen Schnitts tief in das Material gesaugt wird, was zu einer zu schnellen Vertiefung des Lochs, einem Verlust der Kontrolle über den Prozess und sogar zum Bruch des Bohrers führen kann. Um dies zu verhindern, werden Bohrer mit modifizierter Geometrie – mit null oder leicht negativen Spanwinkeln – verwendet. Dadurch wird sichergestellt, dass das Werkzeug das Material tatsächlich schneidet, anstatt sich tief in das Loch „hineinzuziehen”. Das Ergebnis ist ein stabiler Prozess und eine bessere Lochqualität. Das Gewindeschneiden in Messing verläuft reibungslos, solange die Werkzeuge gut auf die Art der Bohrung und die Legierung abgestimmt sind: Kühlung und Schmierung bei der CNC-Bearbeitung von Messing Bei Bleigehalten ist eine Trockenbearbeitung oder eine Bearbeitung mit minimaler Schmierung (MQL) möglich. Aufgrund der kurzen Späne und der hohen Wärmeleitfähigkeit kommt es nicht zu einer übermäßigen Erwärmung des Werkzeugs. Anders verhält es sich bei bleifreien Legierungen, die eine schlechtere Wärmeleitfähigkeit aufweisen. Bei ihrer Bearbeitung ist es entscheidend, eine Emulsions- oder Ölkühlung zu verwenden, die die Standzeit des Werkzeugs erheblich verlängert und die Oberflächenqualität verbessert. Gesundheits- und Sicherheitsaspekte bei der Messingbearbeitung Bei Bleisorten wie CW614N ist es wichtig, sich der Gesundheitsrisiken bewusst zu sein. Das in der Legierung enthaltene Blei verbessert zwar die Bearbeitbarkeit, ist aber auch ein giftiger Stoff. Staub und feine Partikel, die bei der Bearbeitung entstehen, können eingeatmet oder durch Handkontakt auf den Körper übertragen werden. Eine längere Exposition gegenüber Blei ist mit dem Risiko von Störungen des Nervensystems, Durchblutungsstörungen oder Nierenschäden verbunden. Daher sollten Messingverarbeitungsbetriebe Folgendes verwenden: Bei bleifreien Messingen ist dieses Risiko praktisch ausgeschlossen. Zusammenfassung Die CNC-Bearbeitung von Messing ist ein effizientes und relativ einfaches Verfahren, jedoch erfordert jede Materialsorte eine individuelle Herangehensweise. Bleihaltige Messinge bieten eine außergewöhnliche Bearbeitbarkeit, während bleifreie Sorten eine Anpassung der Parameter und eine Kühlung erfordern, jedoch umwelt- und gesundheitsverträglicher sind. Durch die Wahl der richtigen Werkzeuge, Schnittparameter und Kühlsysteme lassen sich Präzisionsteile mit hoher Oberflächenqualität herstellen, wodurch Messing zu einem der wichtigsten Werkstoffe in der modernen industriellen Fertigung wird.
Neue Investition in den Maschinenpark von SIM Gdynia – Laserbeschriftungsmaschine HBS-GQ-20F
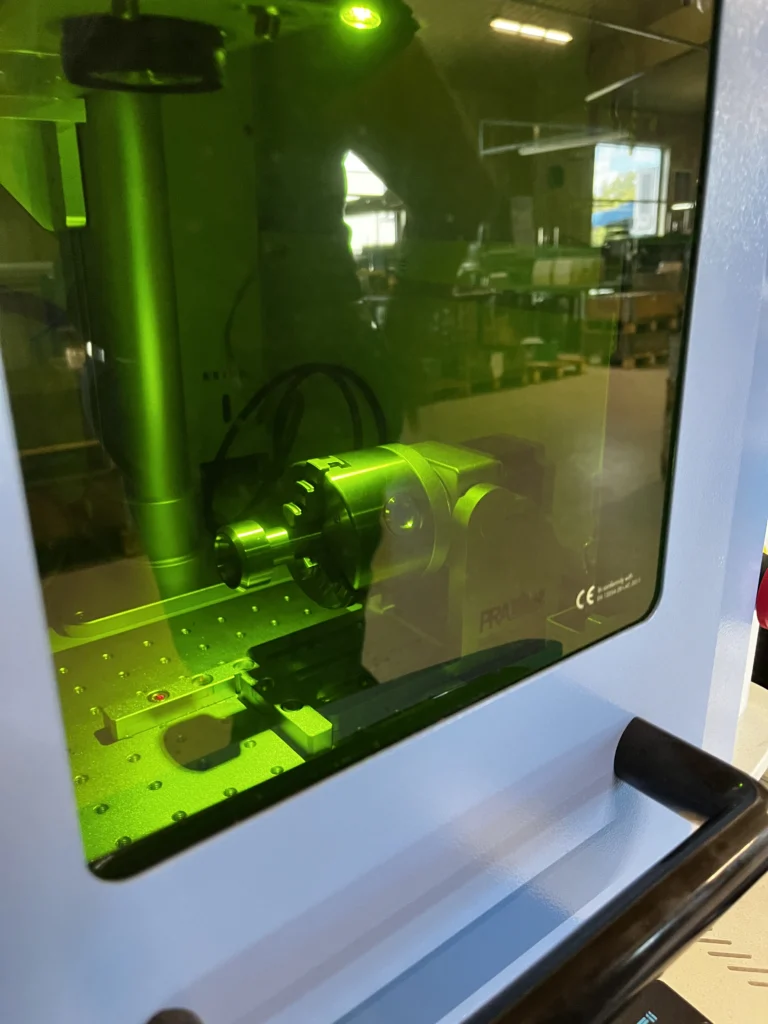
Im Einklang mit dem Zeitgeist und als Reaktion auf die wachsenden Anforderungen des Marktes bei SIM Gdynia haben wir in eine moderne Laserbeschriftungsmaschine HBS-GQ-20F investiert. Dieses mit einem Windows-basierten System ausgestattete Gerät beschleunigt den Prozess der Konfiguration und Einstellung der Arbeitsparameter erheblich, was sich direkt in einer kürzeren Beschriftungszeit niederschlägt – insbesondere bei großen Teileserien. Warum HBS-GQ-20F? Die Laserbeschriftungsmaschine HBS-GQ-20F zeichnet sich durch ihr Design als geschlossene Markierungsstation aus – eine geschlossene Arbeitskammer, die die Sicherheit des Bedieners erhöht und die Handhabung komplexer Teile erleichtert. Dank der geräumigen Konstruktion können Werkstücke mit ungewöhnlichen Formen problemlos platziert und zusätzliches Markierzubehör verwendet werden. Wie der Hersteller betont, ist das Modell GQ-20F ein „Mega-Körper mit Mega-Leistung“ – ein Gerät für den intensiven industriellen Einsatz, das sich sowohl für die Markierung kleiner Komponenten als auch für größere Teile eignet, die eine präzise Gravur erfordern. Wichtige technische Parameter Die neue Maschine bietet uns die Möglichkeit, in verschiedenen Konfigurationen zu markieren, unter anderem mit folgenden Eigenschaften: Die Maschine ist luftgekühlt, was den Betrieb erleichtert und die Wartungskosten senkt. Arbeitet mit gängigen Grafikdateiformaten (.ai, .plt, .dxf, .tiff, .jpg), was eine große Flexibilität bei der Projektvorbereitung ermöglicht. Optionale Linsen – verschiedene Markierungsfelder Je nach Ihren Anforderungen kann die HBS-GQ-20F mit Linsen ausgestattet werden, die Ihnen die Arbeit mit folgenden Markierungsfeldern ermöglichen: Dadurch ist es möglich, sowohl sehr kleine als auch große Bauteile zu markieren, was die Vielseitigkeit des Systems weiter erhöht. Vorteile für die Kunden von SIM Gdynia Der Kauf einer neuen Laserbeschriftungsmaschine ist ein weiterer Schritt in der Entwicklung unseres Maschinenparks. Mit der HBS-GQ-20F können wir Folgendes bieten: Die neue Technologie ermöglicht es uns, die Bedürfnisse von Kunden aus verschiedenen Branchen – vom Maschinenbau über die Energiebranche bis hin zum Medizin- und Verteidigungssektor – besser zu erfüllen.
SIM Gdynia auf der MSPO 2025 – mit neuer Konzession und neuen Möglichkeiten
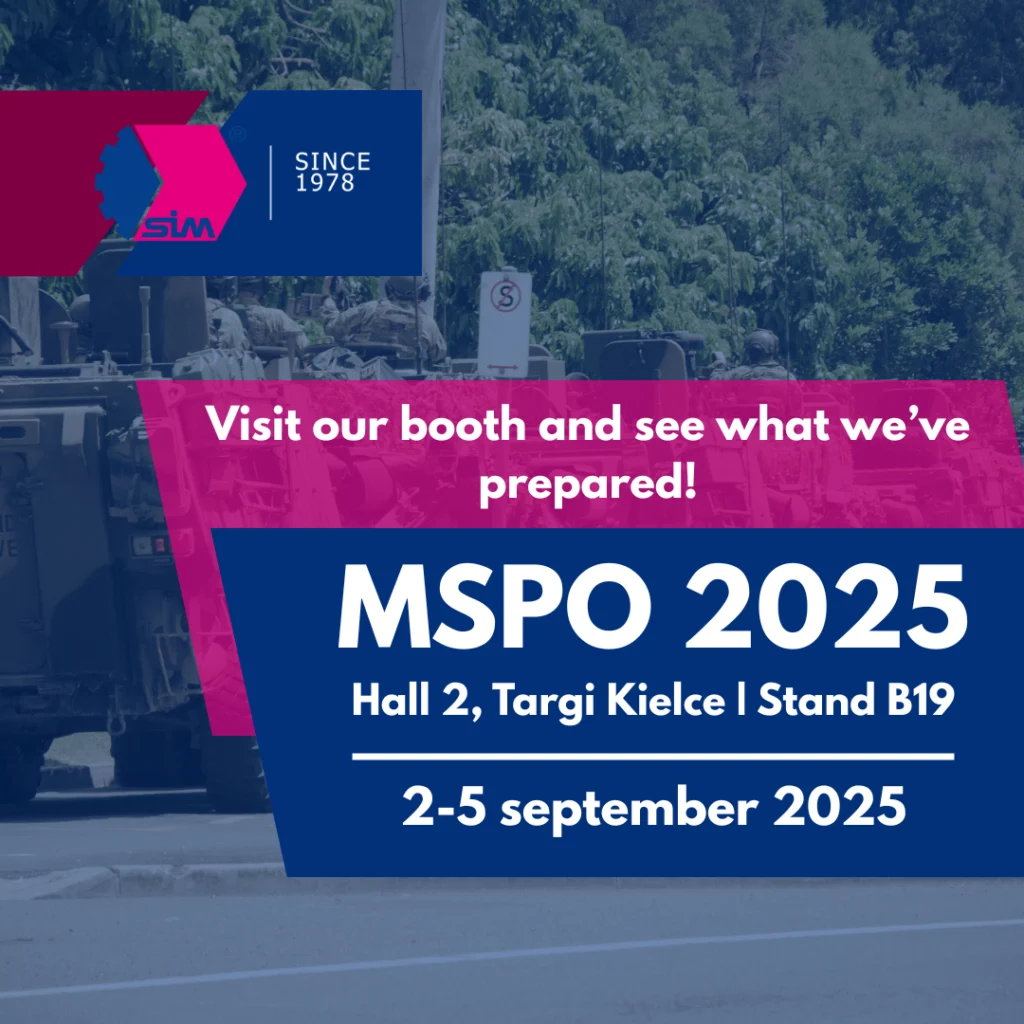
Die MSPO-Messe ist die größte Veranstaltung der Verteidigungsindustrie in Mittel- und Osteuropa, die jedes Jahr die wichtigsten Hersteller, Technologieanbieter und Entscheidungsträger aus der ganzen Welt zusammenbringt. Es ist ein Ort, an dem das Militär auf die Industrie trifft und innovative technologische Lösungen als Antwort auf die wachsenden Anforderungen an Sicherheit und moderne Verteidigung präsentiert werden. Auch in diesem Jahr nehmen wir wieder als Aussteller an der Internationalen Messe für Verteidigungsindustrie teil und präsentieren unsere neuesten Kompetenzen, CNC-Bearbeitungstechnologien und neuen Möglichkeiten, die sich aus der erhaltenen Konzession für die Durchführung von Projekten für den Militärsektor ergeben. MSPO – Treffpunkt für Industrie, Technologie und Sicherheit Die von Targi Kielce organisierte Veranstaltung spielt seit über 30 Jahren eine Schlüsselrolle bei der Gestaltung der Beziehungen zwischen Anbietern von Lösungen für das Militär und Auftraggebern – sowohl nationalen als auch internationalen. An den bisherigen Ausgaben nahmen über 600 Unternehmen aus mehreren Dutzend Ländern teil, und Tausende von Fachleuten, Ingenieuren, Militärdelegationen und Vertretern der staatlichen Verwaltung besuchten die Messehallen. Die MSPO ist nicht nur eine Ausstellung von Ausrüstung und Technologie, sondern auch eine Gelegenheit, konkrete Geschäftskontakte zu knüpfen, über Projekte zu sprechen und die eigenen Möglichkeiten im Kontext der tatsächlichen Bedürfnisse des Verteidigungssektors zu präsentieren. SIM Gdynia – CNC für die Verteidigung Unsere Präsenz auf der MSPO 2025 hat einen besonderen Charakter. Im Juli dieses Jahres haben wir die offizielle Konzession für die Durchführung von Projekten für den Verteidigungssektor erhalten, was unsere Bereitschaft zur Herstellung von Komponenten, die den höchsten Anforderungen in Bezug auf Qualität, Sicherheit und Normkonformität entsprechen, formal bestätigt. Während der Messe präsentieren wir unsere Schlüsselkompetenzen in den Bereichen: Präzise CNC-Bearbeitung von Metall- und Kunststoffteilen, Realisierung komplexer mechanischer Projekte für militärische Anwendungen, Bearbeitung schwieriger Werkstoffe und großformatiger Komponenten, Qualitätskontrolle und Endbearbeitung gemäß den Branchenstandards. Wo Sie uns während der MSPO 2025 finden Wir laden Sie herzlich ein, unseren Stand zu besuchen: Halle 2, Stand B19 2.–5. September 2025 | Targi Kielce Unser Team steht Ihnen gerne zur Verfügung, um Ihnen das Angebot von SIM Gdynia vorzustellen und über Möglichkeiten der Zusammenarbeit im Bereich Militär- und Verteidigungsprojekte zu sprechen. Wir laden Sie zu einem Gespräch über zukunftsweisende Projekte ein SIM Gdynia ist ein Partner für alle, die einen bewährten Auftragnehmer mit Erfahrung, Flexibilität und Zugang zu fortschrittlicher CNC-Technologie suchen. Unsere Teilnahme an der MSPO 2025 ist nicht nur eine Präsentation unseres Angebots, sondern auch eine offene Einladung zum Dialog, zum Wissensaustausch und zur Planung zukunftsweisender Projekte. Wenn Sie an einer Zusammenarbeit im Bereich der Präzisionsbearbeitung von Komponenten für militärische Anwendungen interessiert sind, laden wir Sie ein, sich mit uns in Verbindung zu setzen oder uns während der Messe persönlich zu besuchen. Wir sehen uns in Kielce.
SIM Gdynia hat eine Lizenz für die Herstellung von Waffen und Militärtechnologie erhalten
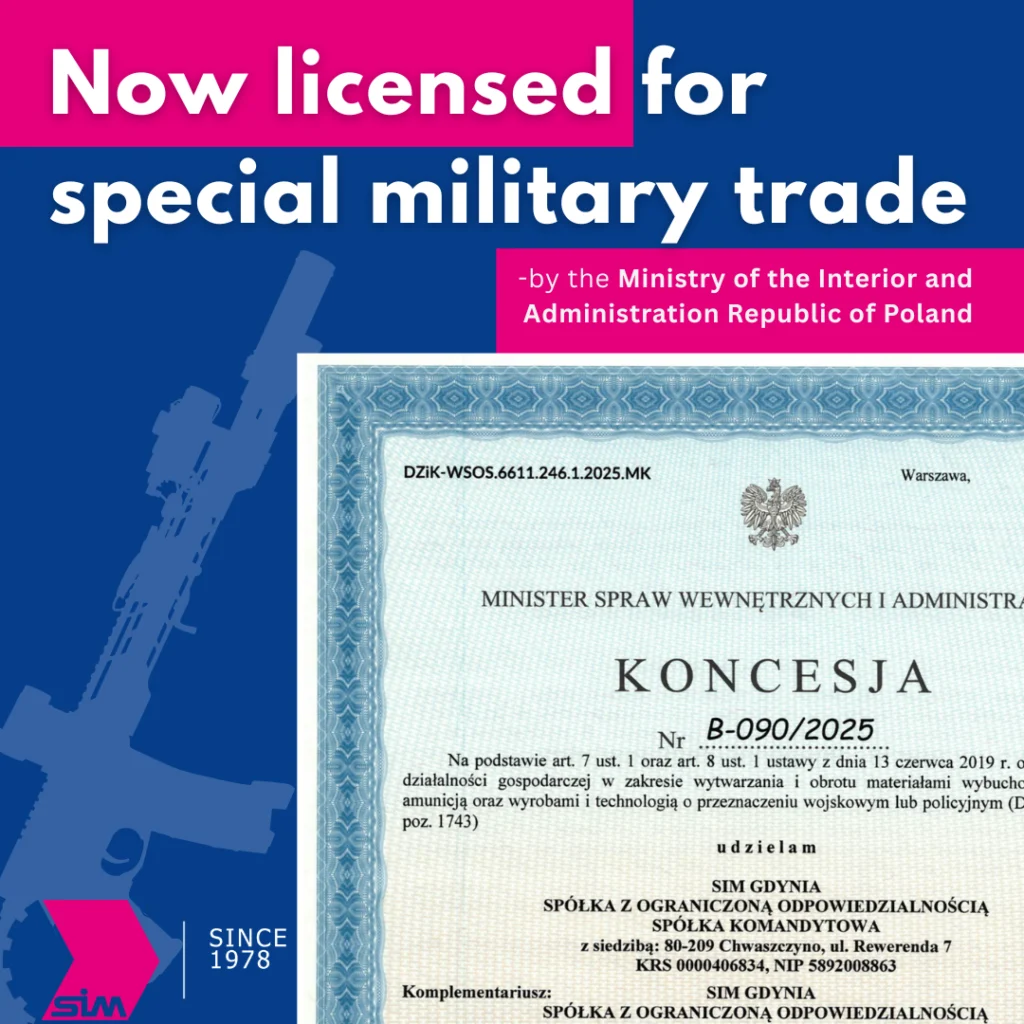
Wir sind stolz darauf, bekannt geben zu dürfen, dass SIM Gdynia Sp. z o.o. Sp.k. vom Ministerium für Inneres und Verwaltung (Nr. B-090/2025) die Konzession für die Ausübung einer wirtschaftlichen Tätigkeit im Bereich der Herstellung und des Handels mit Waffen, Munition, Sprengstoffen sowie Technologien für militärische oder polizeiliche Zwecke erhalten hat. Dies ist ein Meilenstein in unserer Geschichte, der bestätigt, dass SIM Gdynia nicht nur ein erfahrener Hersteller von mechanischen Komponenten ist, sondern auch ein zuverlässiger und voll autorisierter Partner für staatliche Institutionen und Unternehmen im Bereich Sicherheit und Verteidigung. Bestätigung unserer Kompetenz Die Erteilung der Konzession durch das Ministerium für Inneres und Verwaltung ist nicht nur eine Formalität, sondern das Ergebnis einer sorgfältigen Überprüfung unserer Prozesse, Ressourcen und der Einhaltung der Vorschriften in Bezug auf Sicherheit und staatliche Aufsicht. Der Erhalt dieses Dokuments bestätigt die höchsten Betriebsstandards und die vollständige Transparenz unserer Tätigkeit. Für unsere bestehenden und zukünftigen Kunden ist dies ein klares Signal: SIM Gdynia ist ein Partner, der bereit ist, Projekte von strategischer Bedeutung zu realisieren – von einzelnen Komponenten bis hin zu komplexen mechanischen Systemen für den Verteidigungssektor. Bereit für neue Herausforderungen Dank unseres umfangreichen Maschinenparks, unserer Erfahrung in der fortschrittlichen CNC-Bearbeitung und unserer eigenen Forschungs- und Qualitätskontrollabteilung können wir Aufträge ausführen, die höchste Präzision, Vertraulichkeit und die Einhaltung strenger technischer Normen erfordern. Wir verfügen über die technologische Ausstattung, die für die Fertigung sowohl von Prototypen in Kleinserien als auch von kompletten Produktionsserien für militärische und polizeiliche Anwendungen erforderlich ist. Wir laden Sie zur Zusammenarbeit ein Wir sind bereit, Projekte zu unterstützen, die besondere Kompetenzen und Zulassungen erfordern. Wenn Ihr Unternehmen einen bewährten Hersteller von Spezialkomponenten sucht, kontaktieren Sie uns. Wir besprechen gerne die Möglichkeiten einer Zusammenarbeit und passen unser Angebot an die individuellen Anforderungen Ihres Projekts an.
Oberflächenbearbeitung nach der CNC-Bearbeitung – Wissenswertes über den letzten Bearbeitungsschritt
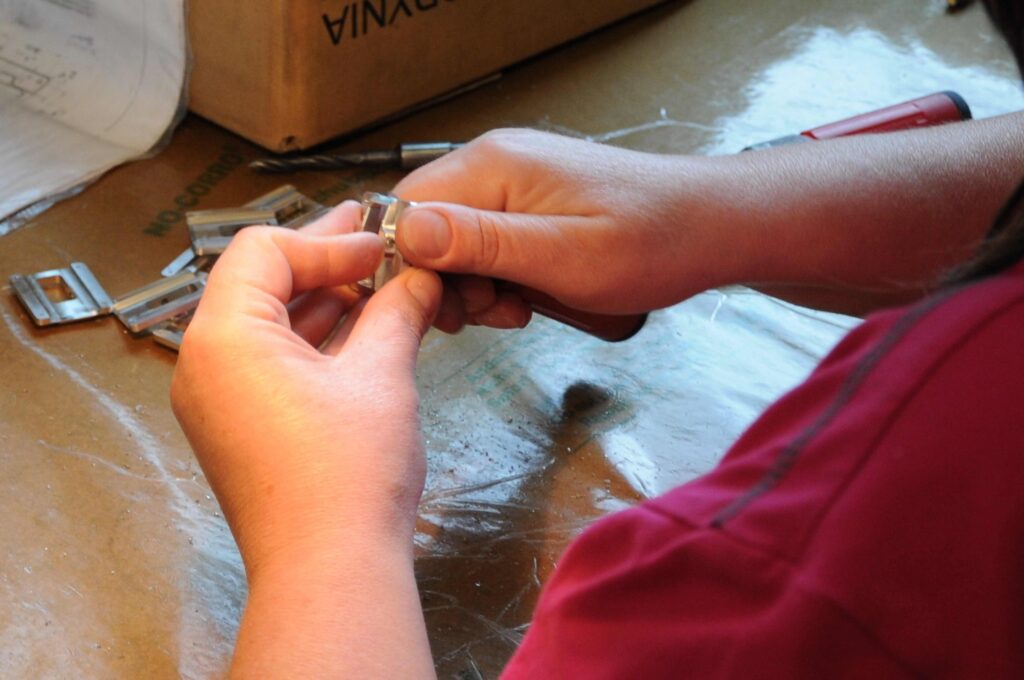
Die CNC-Bearbeitung ist ein Verfahren, mit dem eine präzise Form und die erforderliche Maßgenauigkeit eines Bauteils erreicht werden können. Das fertige Bauteil ist jedoch nicht immer sofort nach dem Fräsen oder Drehen einsatzbereit. Entscheidend für die endgültige Qualität und Funktionalität des Bauteils ist der Prozess der Oberflächenveredelung. Dabei wird die bearbeitete Oberfläche geglättet, gereinigt und an die vorgesehenen Betriebsbedingungen angepasst. Die Wahl der richtigen Veredelungsmethode kann über die Haltbarkeit, Widerstandsfähigkeit und Ästhetik des Bauteils entscheiden. Selbst minimale Grate, Unebenheiten oder Werkzeugspuren können die Funktion technischer Systeme beeinträchtigen und zu Undichtigkeiten, vorzeitigem Verschleiß oder sogar zu Schäden führen. Warum ist die Oberflächenveredelung nach der CNC-Bearbeitung so wichtig? Die richtige Oberflächenveredelung hat einen direkten Einfluss auf die Funktionsparameter von CNC-bearbeiteten Teilen. Unter anderem: Eine gut ausgeführte Endbearbeitung erhöht den Nutzwert des Bauteils erheblich und vermeidet kostspielige Ausfälle während des Betriebs. Übersicht über die Endbearbeitungsverfahren Je nach technischen, ästhetischen und funktionalen Anforderungen werden CNC-bearbeitete Bauteile verschiedenen Endbearbeitungsverfahren unterzogen. Jedes dieser Verfahren hat einen bestimmten Anwendungsbereich und beeinflusst die Endqualität der Oberfläche. Entgraten Entgraten ist ein Verfahren zum Entfernen von Graten und scharfen Kanten. Es kann manuell (z. B. mit Messern, Feilen), mechanisch (mit Bürsten, Fräsern) oder thermisch durchgeführt werden. Es sorgt für sichere und saubere Oberflächen der Teile, die für die weitere Bearbeitung bereit sind. Trommeln Bei dieser Methode werden die Teile zusammen mit Schleifmitteln und einer Flüssigkeit in eine Trommel gegeben. Durch die Drehung des Elements wird eine sanfte Glättung erzielt, wodurch die Oberflächenrauheit beseitigt wird, was ideal für die Serienfertigung ist. Der Prozess verbessert das Aussehen und beseitigt mikroskopisch kleine Unregelmäßigkeiten. Präzisionsschleifen Dies ist ein mechanisches Verfahren, mit dem eine sehr geringe Rauheit (Ra < 0,4 µm) erreicht werden kann. Ideal für Teile, die eine hohe Dichtheit, Passgenauigkeit und Präzision erfordern. Wird z. B. bei Hydraulikkomponenten eingesetzt. Polieren Das Polieren ist das Glätten von Oberflächen mit Pasten und Polierwerkzeugen. Verbessert die Ästhetik und verringert die Verschmutzungsneigung. Schutzbeschichtungen Wie wählt man die richtige Veredelungsmethode? Die Wahl der richtigen Veredelungsmethode hängt von mehreren entscheidenden Faktoren ab: Bei rostfreiem Stahl wird aufgrund der Notwendigkeit, Grate zu entfernen, meist Entgraten verwendet. Bei Aluminium wird meist Eloxieren gewählt, das eine harte und korrosionsbeständige Schutzschicht bildet und gleichzeitig die Ästhetik des Details verbessert. Maschinengehäuse werden in der Regel entgratet, kugelgestrahlt und verzinkt. Hier sind nicht nur die Ästhetik, sondern vor allem die Sicherheit des Benutzers und ein wirksamer Korrosionsschutz, insbesondere in feuchten oder chemisch aggressiven Umgebungen, von Bedeutung. Zusammenfassung Die Oberflächenveredelung ist kein Zusatz, sondern ein Bestandteil des standardmäßigen CNC-Bearbeitungsprozesses. Sie wirkt sich direkt auf die Qualität, Wiederholgenauigkeit und Haltbarkeit des Werkstücks aus. In der industriellen Praxis wird die Oberflächenveredelung als kritischer Faktor angesehen, der über die Zuverlässigkeit des fertigen Bauteils und seine Beständigkeit gegenüber den Betriebsbedingungen entscheidet. Daher sollte die Wahl der geeigneten Methode bereits in der Phase der technologischen Planung erfolgen.
CNC-Stahlbearbeitung – wie bearbeitet man das beliebteste Material in der Fertigung?
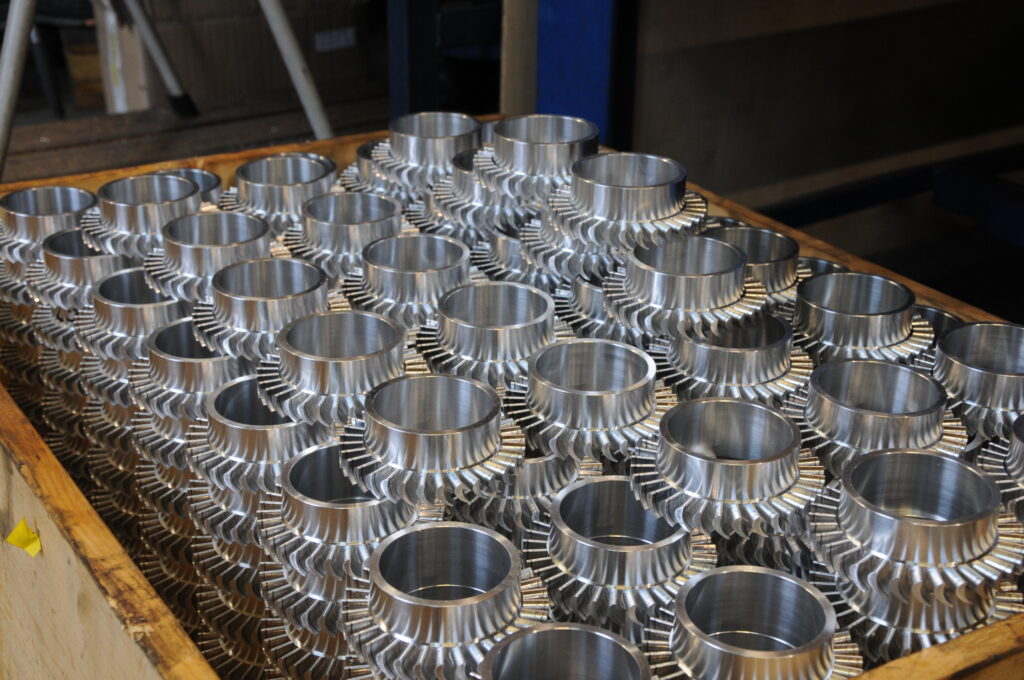
In der Fertigungsindustrie nimmt Stahl eine der wichtigsten Positionen unter den Konstruktionswerkstoffen ein. Seine Beliebtheit beruht auf seiner guten Verfügbarkeit, seinen vielfältigen mechanischen Eigenschaften und der Möglichkeit, seine Struktur durch Legierungszusätze und Wärmebehandlung zu verändern. In der Praxis bedeutet dies, dass zwei scheinbar ähnliche Stahlsorten völlig unterschiedlich auf das Fräsen und Drehen reagieren können. In diesem Artikel betrachten wir die Eigenschaften von Stahl, die sein Verhalten bei der CNC-Bearbeitung von Metallen bestimmen. Wir zeigen, warum die Kenntnis der Materialart keine Formalität ist, sondern die Grundlage für einen gut geplanten technologischen Prozess. Eigenschaften von Stahl und Anwendungen in der modernen CNC-Bearbeitung Stahl ist eine Legierung aus Eisen und Kohlenstoff. Er kann Legierungszusätze wie Chrom, Nickel, Molybdän oder Mangan enthalten. Diese Bestandteile ermöglichen es, unterschiedliche physikalische und chemische Eigenschaften des Materials zu erzielen. Die am häufigsten verwendeten Legierungszusätze für Stahl sind: Die häufigsten Stahlsorten: Die Kenntnis der Eigenschaften einer bestimmten Stahlsorte ist für die Planung der CNC-Bearbeitung von entscheidender Bedeutung. Von ihnen hängt ab, welche Werkzeuge, Parameter und Kühlmittel verwendet werden sollten. Stahlsorten und CNC-Bearbeitung – wie beeinflussen sie die Auswahl der technologischen Parameter? Die Eigenschaften des Materials bestimmen, wie es sich im Kontakt mit dem Werkzeug verhält und welche technologischen Bedingungen für einen stabilen, wiederholbaren Prozess einzuhalten sind. Niedriglegierte Stähle Sie zeichnen sich durch gute Plastizität und leichte Bearbeitbarkeit aus, haben jedoch eine geringere Festigkeit. Sie können mit höheren Vorschüben und geringerem Risiko einer Werkzeugbeschädigung bearbeitet werden. Hochkohlenstoffstähle Sie sind wesentlich härter und verschleißfester, aber schwieriger zu bearbeiten. Sie erfordern eine scharfe Werkzeuggeometrie und eine Verringerung der Schnittgeschwindigkeit, um Überhitzung und Vibrationen zu vermeiden. Legierte Stähle (z.B.mitChrom-, Nickel- oder Molybdänzusatz) Sie zeichnen sich durch erhöhte Festigkeit, Korrosions- oder Verschleißbeständigkeit aus. Sie erfordern eine individuelle technologische Herangehensweise – sowohl bei der Auswahl des Kühlmittels als auch bei der Schnittstrategie. Rostfreie Stähle Schwierig zu bearbeiten aufgrund ihrer Neigung zur Bildung von Aufbauschicht an der Schneide. Der hohe Chrom- und Nickelgehalt erhöht die Korrosionsbeständigkeit, verschlechtert aber gleichzeitig die Zerspanbarkeit. Sehr scharfe Werkzeuge und intensive Kühlung sind erforderlich. Werkzeugstähle Durch Wärmebehandlung erreichen sie eine hohe Härte. Sie erfordern den Einsatz von Werkzeugen mit hoher Verschleißfestigkeit. Der Zusatz von Molybdän und Vanadium verbessert die Überhitzungs- und Verschleißfestigkeit bei intensiver Zerspanung. Werkzeuge und Maschinen für die CNC-Bearbeitung von Stahl In der modernen CNC-Bearbeitung von Stahl kommt eine breite Palette von Spezialwerkzeugen und -maschinen zum Einsatz, die auf die Art des zu bearbeitenden Materials und die Bearbeitungsmethode abgestimmt sind: Es ist wichtig, die Bearbeitungsparameter wie Schnittgeschwindigkeit, Vorschub und Schnitttiefe an die Eigenschaften des Materials anzupassen. Typische Fehler bei der CNC-Bearbeitung von Stahl und Möglichkeiten zu ihrer Behebung Stahl in einer Bearbeitungsumgebung erfordert eine ständige Kontrolle der Parameter und die Anpassung der Werkzeuge an die Art des Materials. Zu den häufigsten Problemen gehören: Um das Fehlerrisiko zu minimieren, sollten Testläufe durchgeführt, eine auf die Stahlsorte abgestimmte Kühlung verwendet und der Prozess mit Schwingungs- und Temperatursensoren überwacht werden. Zusammenfassung – Was Sie über die CNC-Bearbeitung von Stahl wissen sollten Die CNC-Bearbeitung von Stahl ist ein komplexer, aber grundlegender Prozess in der modernen industriellen Fertigung. Um eine hohe Qualität und Wiederholgenauigkeit der Teile zu erzielen, ist es notwendig, die Eigenschaften der jeweiligen Stahlsorte zu verstehen und die entsprechenden Werkzeuge, Zerspanungsstrategien und Arbeitsparameter der Werkzeugmaschine anzupassen. Von entscheidender Bedeutung sind hier die präzise Auswahl der Werkzeuge (Fräser, Wendeschneidplatten, Bohrer), eine effektive Kühlung und die Steifigkeit der CNC-Maschinen. Das Vermeiden typischer Fehler wie Überhitzung der Werkzeuge, schlechte Befestigung oder zu aggressive Schnitte führt zu einer längeren Lebensdauer der Werkzeuge und einer Optimierung des gesamten Prozesses. Der richtige Ansatz für die Stahlbearbeitung ist nicht nur eine Frage der Technik, sondern auch der Effizienz, Qualität und Zuverlässigkeit.
Die neueste Investition in eine Laserbeschriftungsmaschine HBS‑GQ‑20F – noch mehr Möglichkeiten bei SIM Gdynia
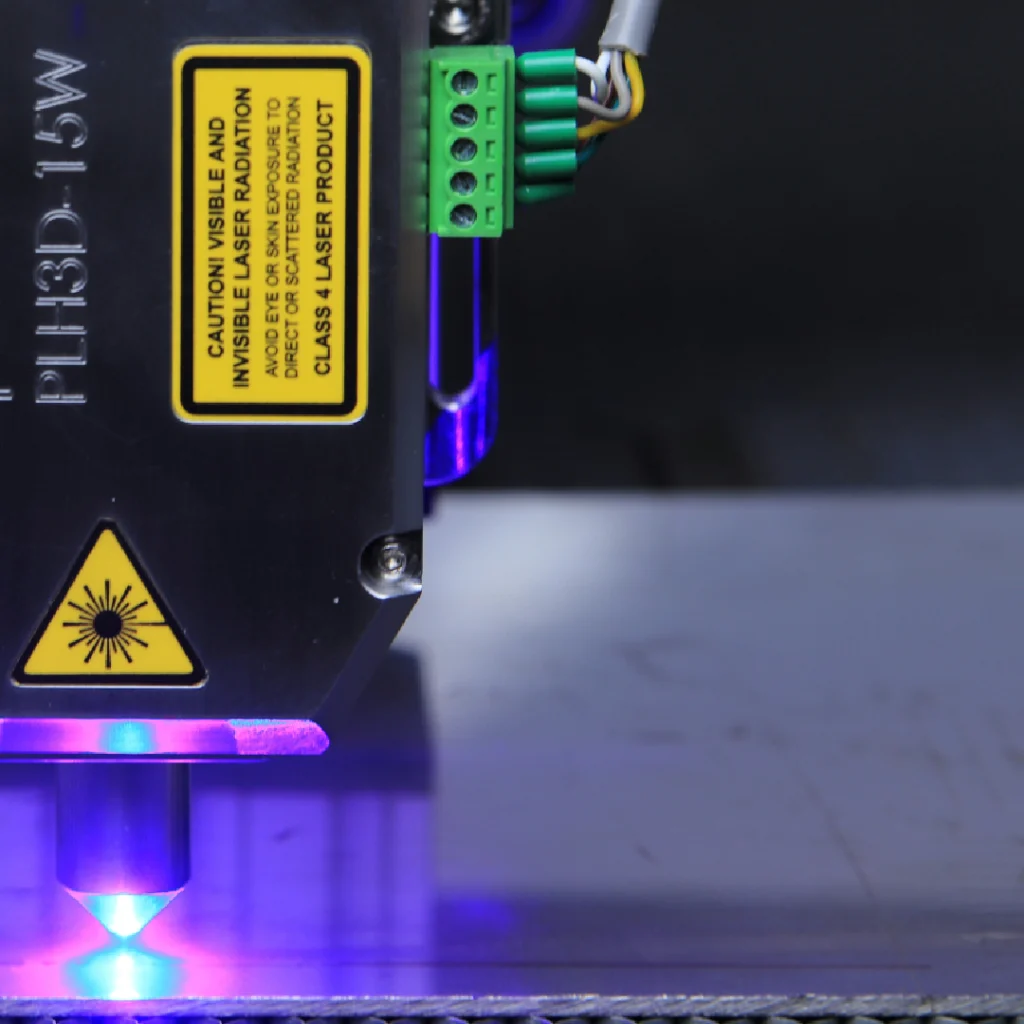
Bei SIM Gdynia investieren wir kontinuierlich in Technologien, die die Präzision, Effizienz und Qualität unserer Dienstleistungen verbessern. Der jüngste Schritt in diese Richtung ist die Anschaffung einer modernen Laserbeschriftungsmaschine HBS‑GQ‑20F. Dieses Gerät ermöglicht uns eine noch effizientere Beschriftung großer Serien von Teilen – mit höherer Genauigkeit und in kürzerer Zeit. Neue Qualität der Markierung bei SIM Gdynia Der Lasermarkierer HBS‑GQ‑20F ist eine moderne Lösung für die präzise Markierung von Metallen und Kunststoffen. Dank seiner geschlossenen Bauweise, der hohen Sicherheitsklasse und der fortschrittlichen Automatisierung passt dieses Gerät ideal zu unseren Produktionsanforderungen. Das integrierte Windows-Betriebssystem ermöglicht eine schnelle und intuitive Konfiguration des Prozesses, was die Produktionsvorbereitung erheblich beschleunigt – insbesondere bei großen Stückzahlen. WichtigetechnischeDatenHBS–GQ–20F Parameter Wert Markierungsbereich 110 × 110 mm (optional: 65 × 65 mm, 170 × 170 mm, 220 × 220 mm, 300 × 300 mm) – je nach verwendeter Linse Markierungstiefe Bis zu 1,2 mm – je nach Material und Anzahl der Durchgänge einstellbar Markierungsgeschwindigkeit Bis zu 12.000 mm/s – sehr schnelle Markierung bei hoher Qualität Positioniergenauigkeit ± 0,001 mm – extrem präzise Wiederholgenauigkeit auch bei großen Serien Laserleistung 20 W, 30 W, 50 W oder 100 W – je nach Bedarf, von der Feinmarkierung bis zur Gravur harter Materialien Lebensdauer der Laserquelle Bis zu 100.000 Stunden – langer Betrieb ohne häufigen Austausch von Bauteilen Stromversorgung/Energieverbrauch 220 V / max. 500 W – niedrige Betriebskosten, Anschluss an eine normale Industriesteckdose Kühlung Luftkühlung – kein Wasser oder zusätzliche Kühlsysteme erforderlich Betriebsbedingungen Temperatur von –10 °C bis +60 °C, Luftfeuchtigkeit 5–95 % – stabiler Betrieb auch unter schwierigen Produktionsbedingungen Unterstützte Dateiformate AI, PLT, DXF, TIFF, JPG und andere – Zusammenarbeit mit gängiger Grafik- und CAD-Software Neuer Standard bei SIM Gdynia Dank dieser Investition können wir mechanische Komponenten schneller, präziser und effizienter als je zuvor kennzeichnen. Das bedeutet Vorteile sowohl für uns als auch für unsere Kunden.
Bericht von der Messe ITM INDUSTRY EUROPE 2025 – SIM Gdynia im Zentrum industrieller Innovationen
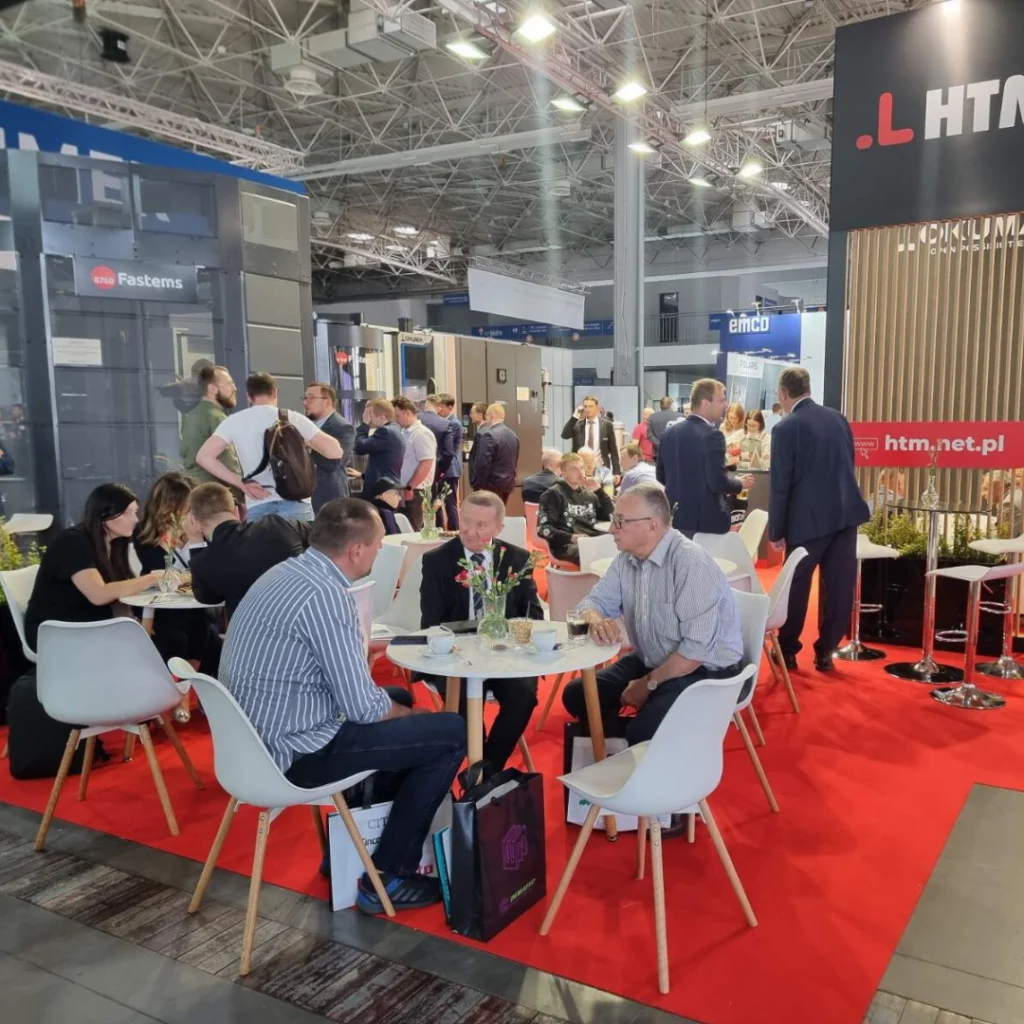
Am 4. Juni 2025 nahmen drei Vertreter unseres Teams an der Messe ITM INDUSTRY EUROPE in Posen teil. Diese Veranstaltung zieht jedes Jahr führende Vertreter der europäischen Industrie an und bietet Raum für den Austausch von Wissen, die Beobachtung von Trends und strategische Kaufentscheidungen. Was ist die ITM INDUSTRY EUROPE? Die ITM INDUSTRY EUROPE ist die größte und umfassendste Industriemesse in Mittel- und Osteuropa. Sie findet in Posen statt und zieht Tausende von Fachleuten aus den Bereichen Metallverarbeitung, Automatisierung, Robotik, Messtechnik und Zukunftstechnologien an. Unter dem gemeinsamen Dach der ITM treffen sich Maschinenhersteller, Systemintegratoren, Ingenieure und führende Anbieter digitaler Lösungen für die Industrie. Im Mittelpunkt der Veranstaltung steht die Industrie 4.0 – also die vollständige Integration von Produktionsprozessen mit digitaler Analytik, Automatisierung und künstlicher Intelligenz. Investitionen und Inspirationen Während unserer Teilnahme an der ITM INDUSTRY EUROPE 2025 hatten wir die Gelegenheit, eine Reihe moderner Lösungen zu analysieren, Technologien zu vergleichen und viele wertvolle Gespräche mit Anbietern von Produktionsunterstützungssystemen zu führen. Wir kehren von diesem Besuch nicht nur mit neuem Wissen, sondern auch mit konkreten Entscheidungen zurück. Wir haben Investitionen getätigt, die in den kommenden Monaten zu weiteren Verbesserungen unserer technologischen und betrieblichen Prozesse führen werden. Dies ist für uns ein strategischer Schritt zur Steigerung der Effizienz und zur Aufrechterhaltung der höchsten Qualitätsstandards, die wir unseren Kunden bieten. Zusammenfassung Die Teilnahme an der ITM 2025 hat bestätigt, dass die Zukunft der Industrie den Unternehmen gehört, die Präzision, Automatisierung und Digitalisierung miteinander verbinden können. Dank unserer Präsenz in Posen verstehen wir die Entwicklungsrichtungen des Marktes und die Bedürfnisse unserer Partner besser. Wir danken den Veranstaltern für die Schaffung eines Raums, der die Entwicklung der Industrie in Polen und Europa wirklich fördert.
Investition in einen eigenen Maschinenpark oder CNC-Outsourcing?
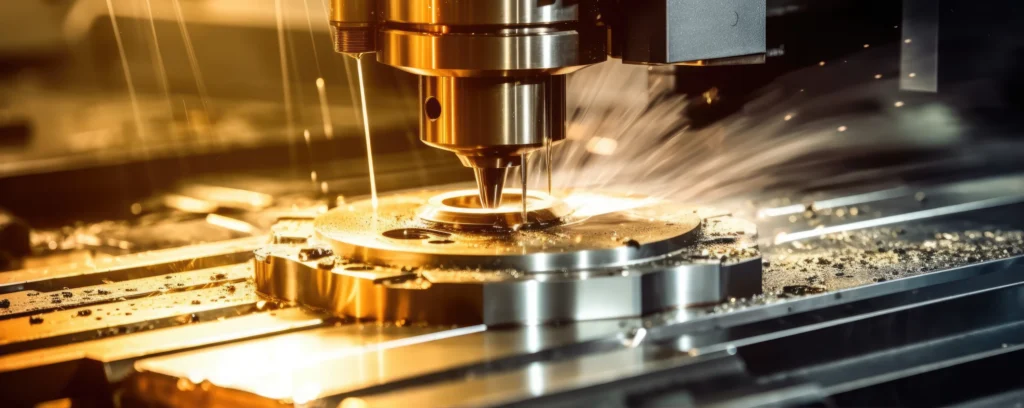
Die Entscheidung, ob ein eigener CNC-Maschinenpark aufgebaut werden soll oder ob die Dienste eines Zulieferers in Anspruch genommen werden sollen, der auf Bestellung mechanische Komponenten herstellt, gehört zu den wichtigsten operativen Entscheidungen in der Industrie. Diese Entscheidung wirkt sich nicht nur auf die Finanzen des Unternehmens aus, sondern auch auf die Zeit bis zur Einführung neuer Produkte, die Verfügbarkeit von Technologien, die operative Flexibilität und das Projektrisiko. Nicht jedes produzierende Unternehmen muss Millionen in moderne Bearbeitungszentren investieren und seine technologische Infrastruktur von Grund auf aufbauen. Andererseits lohnt es sich nicht immer, Prozesse, die für Qualität, Vertraulichkeit und Präzision entscheidend sind, an externe Dienstleister auszulagern. In diesem Artikel analysieren wir beide Ansätze. Die Investition in Maschinen und das Outsourcing der CNC-Bearbeitung, basierend auf konkreten Zahlen, realistischen Szenarien und bewährten Marktpraktiken. Investitionskosten für einen CNC-Maschinenpark–was muss wirklich berücksichtigt werden? Der Kauf einer Maschine ist nur der Anfang. Ein eigener CNC-Maschinenpark verursacht eine Reihe von zusätzlichen Kosten, die bereits in der Investitionsplanungsphase berücksichtigt werden müssen: Es ist zu beachten, dass CAM-Systeme als unbefristete Lizenzen mit einer jährlichen Gebühr für Updates oder im Abonnementmodell angeboten werden können, bei dem die Kosten jährlich anfallen. Die Preisunterschiede ergeben sich aus dem Funktionsumfang, der Anzahl der Achsen der Werkzeugmaschine, dem Zugang zu Simulationen und Postprozessoren. Für ein Beispielzentrum mit 5 Achsen können die jährlichen Betriebskosten – ohne Berücksichtigung der Abschreibung – leicht 400.000 PLN übersteigen. Dies ist eine echte Herausforderung, insbesondere wenn die Maschine nicht unter Volllast arbeitet. Quelle: want.net – CNC Machine Cost Explained Sind 2000 Stunden die Rentabilitätsschwelle? In der Industrie geht man davon aus, dass etwa 2.000 Betriebsstunden pro Jahr die ungefähre Rentabilitätsschwelle für die Investition in eine CNC-Werkzeugmaschine darstellen. Woher kommt diese Zahl? Das entspricht in etwa der Vollauslastung einer Maschine im Einschichtbetrieb: 8 Stunden pro Tag, 5 Tage pro Woche, 50 Wochen pro Jahr (mit einer Reserve für Wartungsausfälle und Feiertage). Oberhalb dieser Grenze beginnt sich die Investition zu amortisieren – die Stückkosten sinken und die Kapitaleffizienz steigt. Je länger die Maschine läuft, desto besser ist der ROI (Return on Investment). In der Praxis ist diese Schwelle jedoch schwer zu erreichen. Marktdaten zeigen, dass die durchschnittliche Auslastung von CNC-Maschinen in Ein-Schicht-Betrieben nur 26 % der verfügbaren Produktionszeit beträgt – also deutlich weniger als die erforderlichen 2.000 Stunden. Dies ist auf unvollständige Auslastung, Ausfallzeiten, Umrüstungen und schwankende Aufträge zurückzuführen. Fazit? 2.000 Stunden sind ein realistisches, aber ehrgeiziges Ziel, das sich nur bei einem regelmäßigen, gut geplanten Produktionsvolumen lohnt. In allen anderen Fällen sollte Outsourcing als Lösung mit geringerem finanziellen Risiko in Betracht gezogen werden. Quelle: https://www.machinemetrics.com/stateoftheindustry2022 Wann lohnt sich eine eigene CNC-Maschinenflotte? Eine eigene CNC-Maschinenflotte ist eine Lösung, die konkrete Vorteile bringen kann. Vor allem dann, wenn: Obwohl einige dieser Anforderungen von externen Auftragnehmern erfüllt werden können, bietet der Besitz eigener Maschinen dem Unternehmen Entscheidungsfreiheit, kürzere Reaktionszeiten und das Potenzial zur Optimierung der Technologie in Echtzeit. Was bietet das Outsourcing der CNC-Bearbeitung? Das Outsourcing der Fertigung mechanischer Komponenten ist heute weit mehr als nur die Vergabe eines Auftrags zur Herstellung eines Teils. Moderne Dienstleistungsunternehmen werden zu Technologiepartnern und bieten Zugang zu Spezialmaschinen, ohne dass eine eigene Infrastruktur von Grund auf aufgebaut werden muss. Im Rahmen einer einzigen Zusammenarbeit erhalten Sie: Wichtig ist auch, dass Outsourcing auch den Zugang zum Erfahrungsschatz eines Teams bedeutet, das seit Jahren Projekte für viele Branchen realisiert. Diese Erfahrung führt zu einer besseren technologischen Beratung, schnelleren Implementierungen und einem geringeren Fehlerrisiko in der Produktionsphase. Wann hat das Outsourcing der CNC-Bearbeitung Vorteile? Outsourcing der CNC-Bearbeitung ist eine Überlegung wert, wenn: Immer mehr Unternehmen nutzen ein gemischtes Modell, bei dem die Kernproduktion im eigenen Haus verbleibt und komplexere oder gelegentliche Aufträge an externe Partner vergeben werden. Zusammenfassung Die Entscheidung, ob Sie einen eigenen Maschinenpark aufbauen oder die CNC-Bearbeitung auslagern sollten, hängt nicht nur von den Stückkosten ab. Es handelt sich um eine strategische Entscheidung, die sich auf das Betriebsmodell, die Kostenstruktur und die Geschwindigkeit der Projektabwicklung auswirkt. Investitionen in Maschinen lohnen sich, wenn ein großes, stabiles Volumen, die Notwendigkeit einer vollständigen Prozesskontrolle und klar definierte technische Kompetenzen innerhalb des Unternehmens vorhanden sind. Dieses Modell bietet Unabhängigkeit, erfordert jedoch Kapital, Planung und eine hohe Maschinenauslastung, um rentabel zu sein. Die Auslagerung der CNC-Bearbeitung ist hingegen eine flexible, skalierbare und finanziell risikoarme Lösung. Sie eignet sich gut für Unternehmen, die mit schwankender Nachfrage zu tun haben, neue Produkte entwickeln oder schnellen Zugang zu Technologien benötigen, deren dauerhafte Einführung sich nicht lohnt.