Die neueste Investition in eine Laserbeschriftungsmaschine HBS‑GQ‑20F – noch mehr Möglichkeiten bei SIM Gdynia
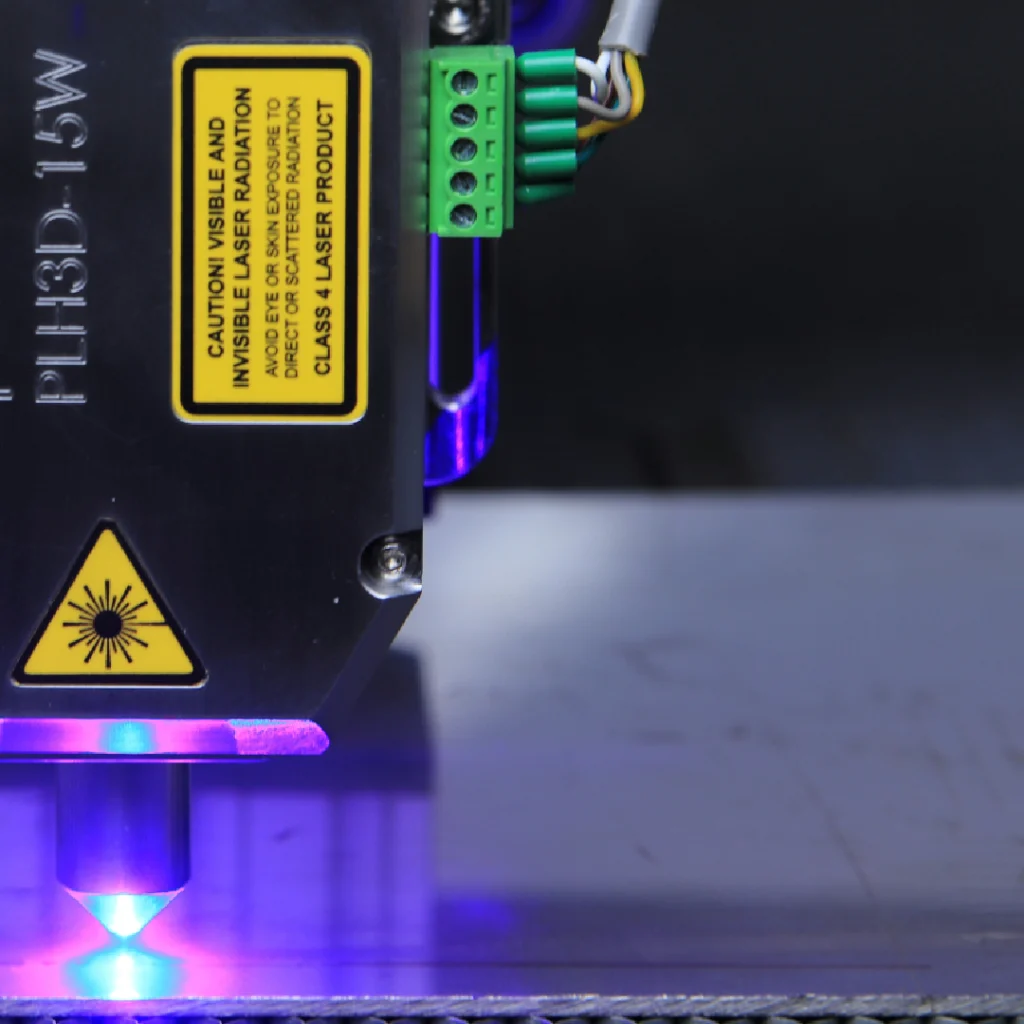
Bei SIM Gdynia investieren wir kontinuierlich in Technologien, die die Präzision, Effizienz und Qualität unserer Dienstleistungen verbessern. Der jüngste Schritt in diese Richtung ist die Anschaffung einer modernen Laserbeschriftungsmaschine HBS‑GQ‑20F. Dieses Gerät ermöglicht uns eine noch effizientere Beschriftung großer Serien von Teilen – mit höherer Genauigkeit und in kürzerer Zeit. Neue Qualität der Markierung bei SIM Gdynia Der Lasermarkierer HBS‑GQ‑20F ist eine moderne Lösung für die präzise Markierung von Metallen und Kunststoffen. Dank seiner geschlossenen Bauweise, der hohen Sicherheitsklasse und der fortschrittlichen Automatisierung passt dieses Gerät ideal zu unseren Produktionsanforderungen. Das integrierte Windows-Betriebssystem ermöglicht eine schnelle und intuitive Konfiguration des Prozesses, was die Produktionsvorbereitung erheblich beschleunigt – insbesondere bei großen Stückzahlen. WichtigetechnischeDatenHBS–GQ–20F Parameter Wert Markierungsbereich 110 × 110 mm (optional: 65 × 65 mm, 170 × 170 mm, 220 × 220 mm, 300 × 300 mm) – je nach verwendeter Linse Markierungstiefe Bis zu 1,2 mm – je nach Material und Anzahl der Durchgänge einstellbar Markierungsgeschwindigkeit Bis zu 12.000 mm/s – sehr schnelle Markierung bei hoher Qualität Positioniergenauigkeit ± 0,001 mm – extrem präzise Wiederholgenauigkeit auch bei großen Serien Laserleistung 20 W, 30 W, 50 W oder 100 W – je nach Bedarf, von der Feinmarkierung bis zur Gravur harter Materialien Lebensdauer der Laserquelle Bis zu 100.000 Stunden – langer Betrieb ohne häufigen Austausch von Bauteilen Stromversorgung/Energieverbrauch 220 V / max. 500 W – niedrige Betriebskosten, Anschluss an eine normale Industriesteckdose Kühlung Luftkühlung – kein Wasser oder zusätzliche Kühlsysteme erforderlich Betriebsbedingungen Temperatur von –10 °C bis +60 °C, Luftfeuchtigkeit 5–95 % – stabiler Betrieb auch unter schwierigen Produktionsbedingungen Unterstützte Dateiformate AI, PLT, DXF, TIFF, JPG und andere – Zusammenarbeit mit gängiger Grafik- und CAD-Software Neuer Standard bei SIM Gdynia Dank dieser Investition können wir mechanische Komponenten schneller, präziser und effizienter als je zuvor kennzeichnen. Das bedeutet Vorteile sowohl für uns als auch für unsere Kunden.
Bericht von der Messe ITM INDUSTRY EUROPE 2025 – SIM Gdynia im Zentrum industrieller Innovationen
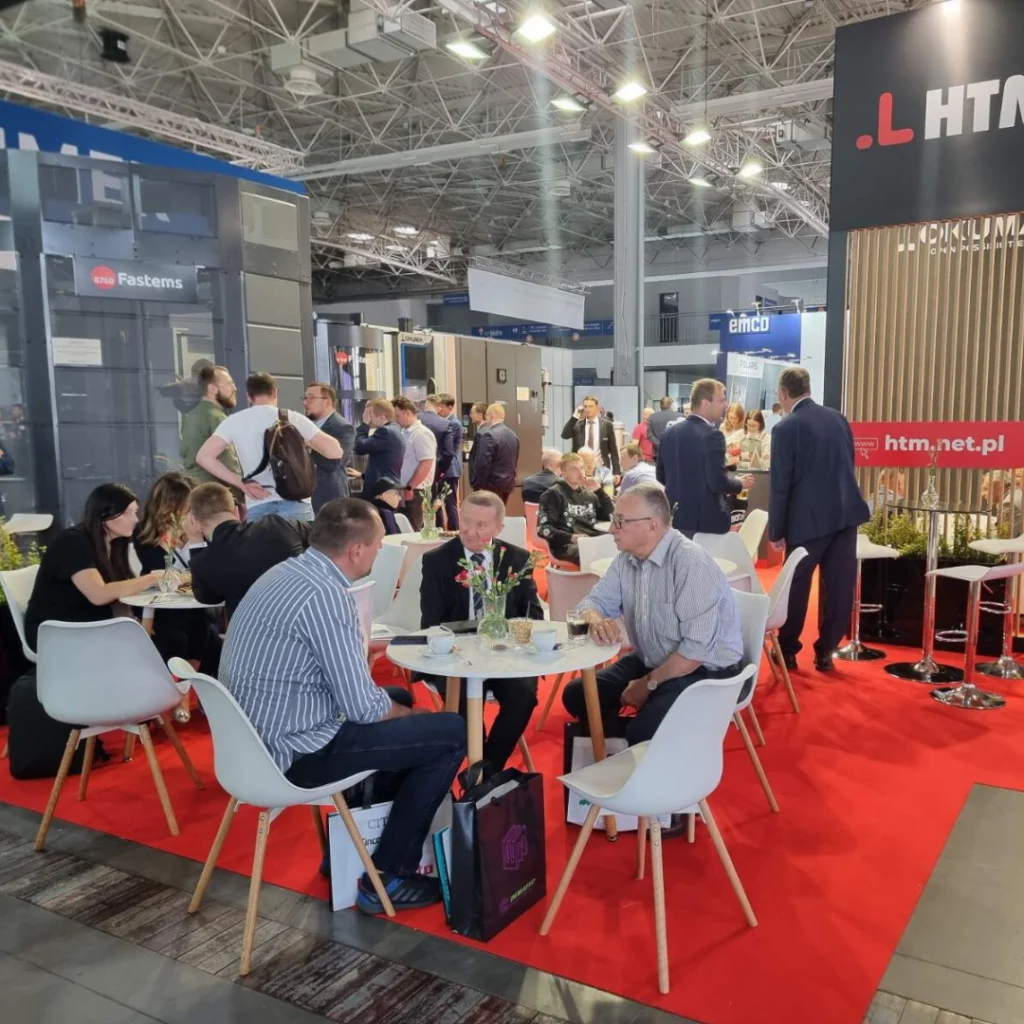
Am 4. Juni 2025 nahmen drei Vertreter unseres Teams an der Messe ITM INDUSTRY EUROPE in Posen teil. Diese Veranstaltung zieht jedes Jahr führende Vertreter der europäischen Industrie an und bietet Raum für den Austausch von Wissen, die Beobachtung von Trends und strategische Kaufentscheidungen. Was ist die ITM INDUSTRY EUROPE? Die ITM INDUSTRY EUROPE ist die größte und umfassendste Industriemesse in Mittel- und Osteuropa. Sie findet in Posen statt und zieht Tausende von Fachleuten aus den Bereichen Metallverarbeitung, Automatisierung, Robotik, Messtechnik und Zukunftstechnologien an. Unter dem gemeinsamen Dach der ITM treffen sich Maschinenhersteller, Systemintegratoren, Ingenieure und führende Anbieter digitaler Lösungen für die Industrie. Im Mittelpunkt der Veranstaltung steht die Industrie 4.0 – also die vollständige Integration von Produktionsprozessen mit digitaler Analytik, Automatisierung und künstlicher Intelligenz. Investitionen und Inspirationen Während unserer Teilnahme an der ITM INDUSTRY EUROPE 2025 hatten wir die Gelegenheit, eine Reihe moderner Lösungen zu analysieren, Technologien zu vergleichen und viele wertvolle Gespräche mit Anbietern von Produktionsunterstützungssystemen zu führen. Wir kehren von diesem Besuch nicht nur mit neuem Wissen, sondern auch mit konkreten Entscheidungen zurück. Wir haben Investitionen getätigt, die in den kommenden Monaten zu weiteren Verbesserungen unserer technologischen und betrieblichen Prozesse führen werden. Dies ist für uns ein strategischer Schritt zur Steigerung der Effizienz und zur Aufrechterhaltung der höchsten Qualitätsstandards, die wir unseren Kunden bieten. Zusammenfassung Die Teilnahme an der ITM 2025 hat bestätigt, dass die Zukunft der Industrie den Unternehmen gehört, die Präzision, Automatisierung und Digitalisierung miteinander verbinden können. Dank unserer Präsenz in Posen verstehen wir die Entwicklungsrichtungen des Marktes und die Bedürfnisse unserer Partner besser. Wir danken den Veranstaltern für die Schaffung eines Raums, der die Entwicklung der Industrie in Polen und Europa wirklich fördert.
Investition in einen eigenen Maschinenpark oder CNC-Outsourcing?
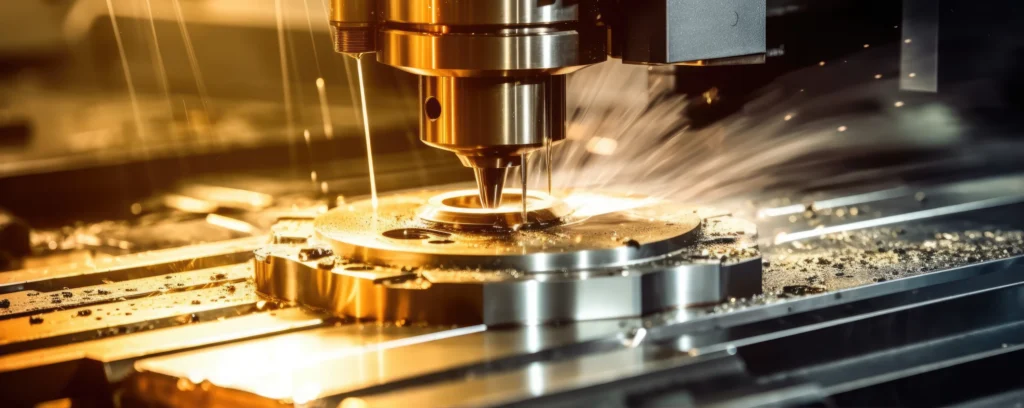
Die Entscheidung, ob ein eigener CNC-Maschinenpark aufgebaut werden soll oder ob die Dienste eines Zulieferers in Anspruch genommen werden sollen, der auf Bestellung mechanische Komponenten herstellt, gehört zu den wichtigsten operativen Entscheidungen in der Industrie. Diese Entscheidung wirkt sich nicht nur auf die Finanzen des Unternehmens aus, sondern auch auf die Zeit bis zur Einführung neuer Produkte, die Verfügbarkeit von Technologien, die operative Flexibilität und das Projektrisiko. Nicht jedes produzierende Unternehmen muss Millionen in moderne Bearbeitungszentren investieren und seine technologische Infrastruktur von Grund auf aufbauen. Andererseits lohnt es sich nicht immer, Prozesse, die für Qualität, Vertraulichkeit und Präzision entscheidend sind, an externe Dienstleister auszulagern. In diesem Artikel analysieren wir beide Ansätze. Die Investition in Maschinen und das Outsourcing der CNC-Bearbeitung, basierend auf konkreten Zahlen, realistischen Szenarien und bewährten Marktpraktiken. Investitionskosten für einen CNC-Maschinenpark–was muss wirklich berücksichtigt werden? Der Kauf einer Maschine ist nur der Anfang. Ein eigener CNC-Maschinenpark verursacht eine Reihe von zusätzlichen Kosten, die bereits in der Investitionsplanungsphase berücksichtigt werden müssen: Es ist zu beachten, dass CAM-Systeme als unbefristete Lizenzen mit einer jährlichen Gebühr für Updates oder im Abonnementmodell angeboten werden können, bei dem die Kosten jährlich anfallen. Die Preisunterschiede ergeben sich aus dem Funktionsumfang, der Anzahl der Achsen der Werkzeugmaschine, dem Zugang zu Simulationen und Postprozessoren. Für ein Beispielzentrum mit 5 Achsen können die jährlichen Betriebskosten – ohne Berücksichtigung der Abschreibung – leicht 400.000 PLN übersteigen. Dies ist eine echte Herausforderung, insbesondere wenn die Maschine nicht unter Volllast arbeitet. Quelle: want.net – CNC Machine Cost Explained Sind 2000 Stunden die Rentabilitätsschwelle? In der Industrie geht man davon aus, dass etwa 2.000 Betriebsstunden pro Jahr die ungefähre Rentabilitätsschwelle für die Investition in eine CNC-Werkzeugmaschine darstellen. Woher kommt diese Zahl? Das entspricht in etwa der Vollauslastung einer Maschine im Einschichtbetrieb: 8 Stunden pro Tag, 5 Tage pro Woche, 50 Wochen pro Jahr (mit einer Reserve für Wartungsausfälle und Feiertage). Oberhalb dieser Grenze beginnt sich die Investition zu amortisieren – die Stückkosten sinken und die Kapitaleffizienz steigt. Je länger die Maschine läuft, desto besser ist der ROI (Return on Investment). In der Praxis ist diese Schwelle jedoch schwer zu erreichen. Marktdaten zeigen, dass die durchschnittliche Auslastung von CNC-Maschinen in Ein-Schicht-Betrieben nur 26 % der verfügbaren Produktionszeit beträgt – also deutlich weniger als die erforderlichen 2.000 Stunden. Dies ist auf unvollständige Auslastung, Ausfallzeiten, Umrüstungen und schwankende Aufträge zurückzuführen. Fazit? 2.000 Stunden sind ein realistisches, aber ehrgeiziges Ziel, das sich nur bei einem regelmäßigen, gut geplanten Produktionsvolumen lohnt. In allen anderen Fällen sollte Outsourcing als Lösung mit geringerem finanziellen Risiko in Betracht gezogen werden. Quelle: https://www.machinemetrics.com/stateoftheindustry2022 Wann lohnt sich eine eigene CNC-Maschinenflotte? Eine eigene CNC-Maschinenflotte ist eine Lösung, die konkrete Vorteile bringen kann. Vor allem dann, wenn: Obwohl einige dieser Anforderungen von externen Auftragnehmern erfüllt werden können, bietet der Besitz eigener Maschinen dem Unternehmen Entscheidungsfreiheit, kürzere Reaktionszeiten und das Potenzial zur Optimierung der Technologie in Echtzeit. Was bietet das Outsourcing der CNC-Bearbeitung? Das Outsourcing der Fertigung mechanischer Komponenten ist heute weit mehr als nur die Vergabe eines Auftrags zur Herstellung eines Teils. Moderne Dienstleistungsunternehmen werden zu Technologiepartnern und bieten Zugang zu Spezialmaschinen, ohne dass eine eigene Infrastruktur von Grund auf aufgebaut werden muss. Im Rahmen einer einzigen Zusammenarbeit erhalten Sie: Wichtig ist auch, dass Outsourcing auch den Zugang zum Erfahrungsschatz eines Teams bedeutet, das seit Jahren Projekte für viele Branchen realisiert. Diese Erfahrung führt zu einer besseren technologischen Beratung, schnelleren Implementierungen und einem geringeren Fehlerrisiko in der Produktionsphase. Wann hat das Outsourcing der CNC-Bearbeitung Vorteile? Outsourcing der CNC-Bearbeitung ist eine Überlegung wert, wenn: Immer mehr Unternehmen nutzen ein gemischtes Modell, bei dem die Kernproduktion im eigenen Haus verbleibt und komplexere oder gelegentliche Aufträge an externe Partner vergeben werden. Zusammenfassung Die Entscheidung, ob Sie einen eigenen Maschinenpark aufbauen oder die CNC-Bearbeitung auslagern sollten, hängt nicht nur von den Stückkosten ab. Es handelt sich um eine strategische Entscheidung, die sich auf das Betriebsmodell, die Kostenstruktur und die Geschwindigkeit der Projektabwicklung auswirkt. Investitionen in Maschinen lohnen sich, wenn ein großes, stabiles Volumen, die Notwendigkeit einer vollständigen Prozesskontrolle und klar definierte technische Kompetenzen innerhalb des Unternehmens vorhanden sind. Dieses Modell bietet Unabhängigkeit, erfordert jedoch Kapital, Planung und eine hohe Maschinenauslastung, um rentabel zu sein. Die Auslagerung der CNC-Bearbeitung ist hingegen eine flexible, skalierbare und finanziell risikoarme Lösung. Sie eignet sich gut für Unternehmen, die mit schwankender Nachfrage zu tun haben, neue Produkte entwickeln oder schnellen Zugang zu Technologien benötigen, deren dauerhafte Einführung sich nicht lohnt.
Leicht, aber anspruchsvoll – wie man die CNC-Bearbeitung von Aluminium erfolgreich durchführt
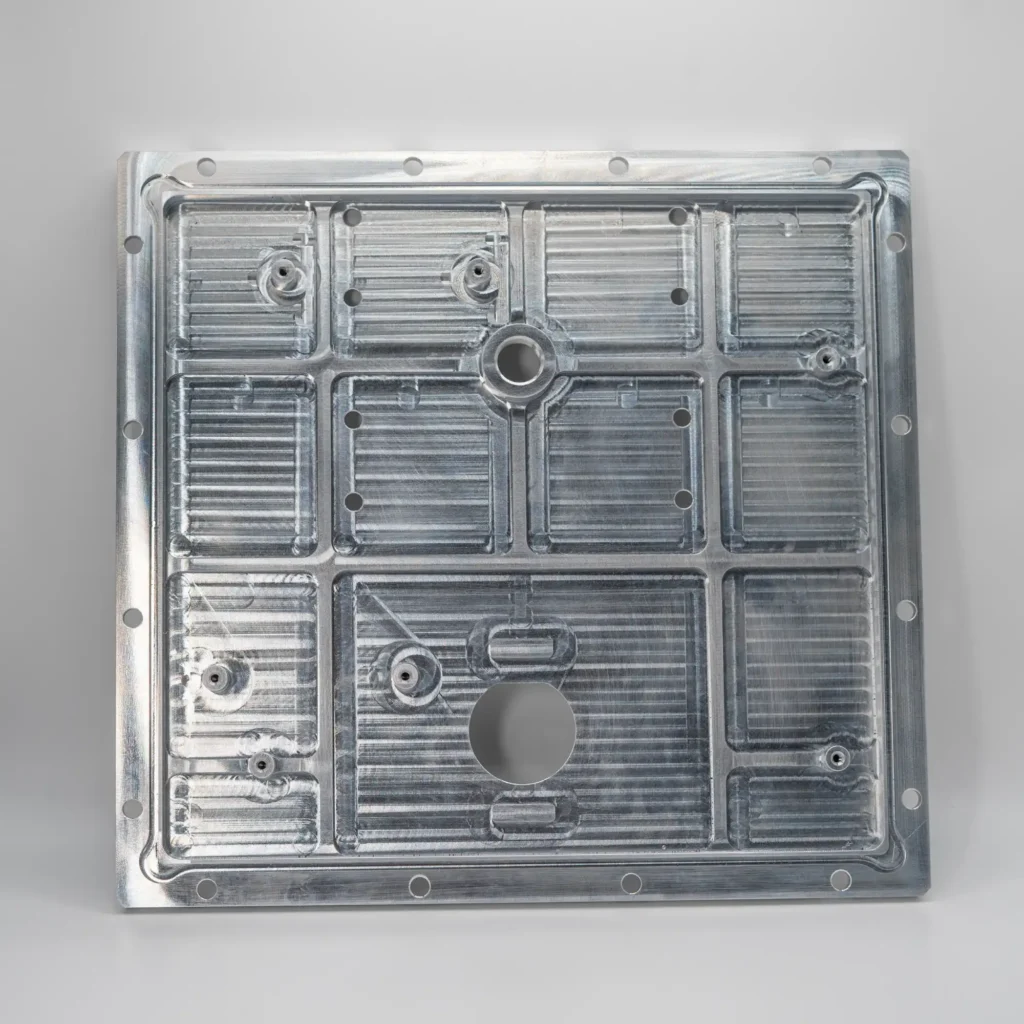
Aluminium ist ein Material, das in der Herstellung mechanischer Komponenten weit verbreitet ist. Seine Leichtigkeit, Korrosionsbeständigkeit und sein günstiges Verhältnis von Festigkeit zu Gewicht machen es ideal für präzise technische Anwendungen. Aber was Aluminium zu einem so attraktiven Material macht, erfordert auch eine über das Übliche hinausgehende Bearbeitung. CNC-Bearbeitung ist heute auch bei der Arbeit mit Aluminium die Grundlage der modernen Fertigung. Die Effizienz des gesamten Prozesses hängt jedoch von vielen Faktoren ab. Von der Auswahl der Werkzeuge und Beschichtungen über die Schnittparameter bis hin zur Art der Kühlung. Genau diese Faktoren entscheiden über die Oberflächenqualität, Wiederholgenauigkeit und Langlebigkeit des fertigen Werkstücks. Auf der Grundlage unserer langjährigen Erfahrung in der CNC-Metallbearbeitung beschreiben wir in diesem Artikel konkrete Lösungen, die sich in der Produktion bewährt haben und eine stabile Qualität des fertigen Werkstücks gewährleisten. Aluminium – Materialspezifikation und Probleme bei der CNC-Bearbeitung Bevor wir uns mit der Zerspanungsstrategie befassen, lohnt es sich, einen Blick auf die Eigenschaften von Aluminium zu werfen, die sich direkt auf die Wahl der Bearbeitungsparameter auswirken. Ihr Verständnis ist entscheidend für die Stabilität und Wiederholbarkeit des gesamten Prozesses. Eigenschaften des Materials Was bedeutet das in der Praxis? Geringe Dichte (2,6–2,8 g/cm³) Aluminium ist leicht, was höhere Drehzahlen und Vorschübe ermöglicht, ohne dass die Maschine so stark belastet wird wie bei Stahl. Hohe Wärmeleitfähigkeit Die Wärme wird schnell aus der Zerspanungszone abgeleitet, gelangt jedoch hauptsächlich in das Werkzeug. Ohne eine effiziente Kühlung überhitzen sich die Schneiden und verschleißen schneller. Geringe Härte (HV ≈ 25–120) Es können scharfe Werkzeuge mit großem Spanwinkel verwendet werden. Die Zerspanung erfolgt flüssig und die Belastung der Werkzeugmaschine bleibt gering. Viskosität und Adhäsion Aluminium neigt dazu, an der Schneide zu haften. Abhilfe schaffen hier reibungsmindernde Beschichtungen, polierte Spanräume und eine gut abgestimmte Kühlung. Obwohl das Drehen und Fräsen von Aluminium auf den ersten Blick „einfach” erscheint, erfordert es in der Praxis viel Aufmerksamkeit und technologische Präzision. Aluminiumlegierungen und ihre Bearbeitbarkeit mit CNC-Technologie Nicht jedes Aluminium verhält sich in Kontakt mit dem Werkzeug gleich. Je nach chemischer Zusammensetzung und Härtungsgrad können unterschiedliche Legierungen völlig unterschiedliche Schnittparameter erfordern – von der Geschwindigkeit über die Kraft bis hin zur optimalen Spindeldrehzahl, Steuerung und dem Schneidwerkzeug. Nachfolgend einige Beispiele für gängige Legierungen in der Herstellung von Aluminiumkomponenten: Die Kenntnis der Aluminiumlegierung erleichtert die Bearbeitung des Materials. Ohne diese Kenntnis ist es schwierig, die richtigen Werkzeuge auszuwählen, die Schnittparameter einzustellen und das Verhalten des Werkstücks während der Fertigung vorherzusagen. Die wichtigsten Verfahren und Arten der CNC-Bearbeitung von Aluminium Aluminium kann je nach den Anforderungen des jeweiligen Projekts und den erwarteten Ergebnissen auf verschiedene Weise effektiv bearbeitet werden. CNC-Fräsen Eignet sich sowohl für Präzisionsteile als auch für große Baublöcke. Das gleichläufige Fräsen sorgt für eine bessere Oberflächenqualität, das gegenläufige Fräsen eignet sich dort, wo Stabilität erforderlich ist. Bei größeren Materialmengen wird das Vollfräsen eingesetzt. Dünnwandige Teile werden mit minimalem Aufmaß und gut abgestimmter Kühlung bearbeitet. CNC-Drehen Wird für achsensymmetrische Teile verwendet: Wellen, Hülsen, Ringe. Beim Drehen ist es wichtig, einen stabilen Vorschub und einen geeigneten Schneidenradius beizubehalten, insbesondere bei dünnwandigen Teilen. Bei zu geringen Schnittparametern entstehen Vibrationen und eine unregelmäßige Oberfläche. Bei zu aggressiven Parametern kommt es zu übermäßiger Spanbildung und der Gefahr der Verformung des Werkstücks. Bohren und Gewindeschneiden Das häufigste Problem sind Grate und Verformungen der Bohrungen. Es werden Bohrer mit einem größeren Spitzenwinkel und guter Spanabfuhr verwendet. Beim Gewindeschneiden haben sich Formgewindebohrer bewährt – sie schneiden nicht, sondern formen das Gewinde. Dadurch werden Späne vermieden und die Verbindung wird verstärkt, insbesondere bei dünnwandigen Bauteilen. Schleifen und Oberflächenvorbereitung Bei der Eloxierung ist die Oberflächenqualität von entscheidender Bedeutung. Jeder Kratzer ist nach der Oxidation sichtbar. Daher werden die Teile häufig einer zusätzlichen Endbearbeitung unterzogen – Fertigfräsen oder Schleifen mit Emulsionen und feinkörnigen Schleifmitteln. CNC-Werkzeuge für die Zerspanung von Aluminium Bei Aluminium ist es entscheidend, Werkzeuge zu verwenden, die eine effektive Spanabfuhr ermöglichen und das Risiko von Materialablagerungen an der Schneidkante verringern. Die am häufigsten verwendeten Werkzeugtypen sind: Die Auswahl des Werkzeugs hängt vom technologischen Arbeitsgang, der Werkstückgeometrie und den Qualitätsanforderungen ab. Jedes Werkzeug hat seine Besonderheiten und eignet sich am besten für bestimmte Anwendungen. Kühlung und Schmierung von Aluminium während des Bearbeitungsprozesses Die CNC-Bearbeitung von Aluminium erfordert besondere Aufmerksamkeit hinsichtlich der Kühlung, da Aluminium die Wärme schnell an die Werkzeuge weiterleitet. Eine unzureichende Kühlung führt schnell zu einer Verschlechterung der Oberflächenqualität der Teile, beschleunigt den Werkzeugverschleiß und kann zu thermischen Verformungen des Werkstücks führen. Die am häufigsten verwendeten Kühl- und Schmiermethoden sind: Moderne Strategien für die Zerspanung von Aluminium Einer der beliebtesten Ansätze ist HPC (High Performance Cutting) – eine Technik zum Tiefschneiden mit geringer Schneidenbreite. Sie ermöglicht eine deutliche Erhöhung der Vorschubgeschwindigkeit, ohne dass die Gefahr einer Überlastung des Werkzeugs oder einer Verschlechterung der Werkstückparameter besteht. Für dünnwandige Aluminiumkomponenten eignet sich HSC (High Speed Cutting) hervorragend. Dank sehr hoher Drehzahlen und geringer Schnittkräfte gewährleistet dieses Verfahren präzises Fräsen ohne Verformung selbst empfindlicher Strukturen. Immer häufiger kommt auch das Trochoidfräsen zum Einsatz – eine Strategie, bei der das Werkzeug auf einer gekrümmten, dynamischen Bahn geführt wird. Dies sorgt für einen gleichmäßigen Verschleiß der Schneiden, eine bessere Kühlung und minimiert mechanische und thermische Belastungen. Fazit – Aluminium zahlt sich durch Präzision aus Aluminium ist ein Werkstoff mit großem Potenzial, aber auch komplexen technologischen Eigenschaften. Um eine wiederholbare Qualität und hohe Effizienz in der CNC-Bearbeitung zu erreichen, reicht eine gute Maschine nicht aus. Es sind gut ausgewählte Werkzeuge, durchdachte Zerspanungsstrategien, eine effektive Kühlung und die Kenntnis der Eigenschaften der jeweiligen Legierung erforderlich. Genau dieser Ansatz – basierend auf Praxis und Erfahrung – ermöglicht es, das Potenzial von Aluminium voll auszuschöpfen und typische Produktionsprobleme zu vermeiden.
CNC-Metallbearbeitung – Grundlage für präzise industrielle Fertigung
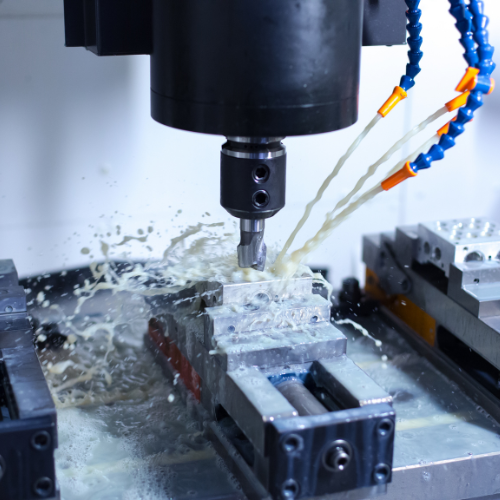
Metalle bilden seit Jahrhunderten die Grundlage für Konstruktionen in der Industrie. Ihre Festigkeit, Leitfähigkeit und Bearbeitbarkeit machen sie für viele Anwendungen unersetzlich. InderFertigungsindustriereicht„guteQualität“nicht mehr aus – heute zählen mikrometrische Präzision, Wiederholgenauigkeit in jeder Serie und Flexibilität bei Designänderungen. Unter diesen Bedingungen werden traditionelle Bearbeitungsmethoden zu einem Hindernis für die Entwicklung. An ihre Stelle treten Lösungen, die Automatisierung mit Zuverlässigkeit verbinden – allen voran die CNC-Bearbeitung, deren Funktionsweise wir im Artikel „Was ist CNC-Bearbeitung?“ ausführlich erklären. Ablauf des Prozesses – wie sieht die Metallbearbeitung auf CNC-Maschinen aus? Der Prozess beginnt mit der Erstellung der technischen Dokumentation im CAD-Format (Computer-Aided Design), die anschließend in einen CAM-Code (Computer-Aided Manufacturing) umgewandelt wird. Dieser Code enthält Anweisungen für die CNC-Maschine bezüglich der Werkzeugbahn, der Drehzahl, des Vorschubs und anderer Parameter. Die Genauigkeit dieser Daten ist entscheidend für das Erreichen des gewünschten Endergebnisses. In dieser Phase erfolgt die eigentliche Metallbearbeitung auf CNC-Maschinen. Die Auswahl der Werkzeuge, der Schnittparameter und der Bearbeitungsstrategien hängt von der Geometrie des Werkstücks, dem Material und der Art des technologischen Vorgangs ab. Moderne CNC-Zentren sind häufig mit automatischen Werkzeugwechslern, Kühlsystemen und Messsensoren ausgestattet, wodurch eine hohe Wiederholgenauigkeit, kurze Produktionszeiten und ein minimiertes Fehlerrisiko gewährleistet sind. Nach den Hauptbearbeitungsschritten folgt die Oberflächenbearbeitung, die Folgendes umfassen kann: Die Qualitätskontrolle in dieser Phase ist entscheidend für die Einhaltung der technischen Anforderungen. Herausforderungen bei der CNC-Bearbeitung von Metallen Jedes Material reagiert anders auf die spanende Bearbeitung. Was bei Stahl funktioniert, kann bei Aluminium oder Messing völlig ungeeignet sein. Die richtige Auswahl der Werkzeuge und Strategien ist der Schlüssel zu Qualität, Wiederholbarkeit und Langlebigkeit des Prozesses. Baustahl (z. B. S235, S355) Dies ist eine der einfacheren Materialgruppen in Bezug auf die Bearbeitung. Es können sowohl HSS-Werkzeuge (High-Speed Steel – Schnellarbeitsstahl) als auch Hartmetallwerkzeuge verwendet werden. Baustahl lässt sich schnell und ohne große Einschränkungen bearbeiten, bei längeren Bearbeitungen sollte jedoch regelmäßig der Verschleiß der Werkzeugschneiden überprüft werden. Edelstahl (z. B. AISI 304, 316) Erfordert eine durchdachte Vorgehensweise. Er ist hart und gleichzeitig „dehnbar“ – er neigt dazu, an der Schneide anzuhaften. Dies führt zu Problemen bei der Spanabfuhr und zu einem beschleunigten Verschleiß des Werkzeugs. Für die Bearbeitung werden in der Regel Schneiden mit reibungsmindernden Beschichtungen empfohlen, z. B. AlTiN (Titannitrid und Aluminium). Gehärteter Stahl (>45 HRC) Für gehärteten Stahl sind Vollhartmetallwerkzeuge (VHM) und geeignete Beschichtungen, z. B. TiSiN (Titannitrid und Silizium), erforderlich, die die Verschleiß- und Temperaturbeständigkeit erhöhen. Der Prozess muss stabil sein – starre Befestigung, kurze Verfahrwege, präzise Bahnführung. Die Parameter müssen sinnvoll gewählt werden, abhängig vom Werkzeugdurchmesser, der Geometrie und den Möglichkeiten der Maschine. Aluminium Aluminium ist ein gut bearbeitbares Material, erfordert jedoch aufgrund seiner Zähigkeit und geringen Härte eine geeignete Vorgehensweise. Bei der Bearbeitung entstehen lange Späne, die den Spaltraum leicht verstopfen, und bei der Bearbeitung dünnwandiger Teile besteht die Gefahr von Vibrationen und Verformungen. Die besten Ergebnisse werden mit Vollhartmetallfräsern (VHM) mit großem Spanwinkel (ca. 45°) und polierter Spanfläche erzielt. Messing und Kupfer Diese Werkstoffe sind sehr gut zerspanbar und gelten oft als „leicht“ in der CNC-Bearbeitung. Ein zu aggressiver Spanwinkel oder eine zu raue Schneidfläche können zu Materialaufrauhung, lokaler Überhitzung der Schneidkante und erhöhtem Verschleiß führen. Dies liegt daran, dass die bei der Bearbeitung entstehende Wärme sehr schnell auf das Werkstück übertragen wird, was bei dünnwandigen Bauteilen zu Verformungen oder Maßänderungen führen kann. Für die CNC-Bearbeitung von Messing oder Kupfer werden Vollhartmetallfräser (VHM) mit sehr scharfen, präzise geschliffenen Schneiden und einer möglichst glatten Oberfläche empfohlen. Das Verständnis der physikalischen und chemischen Eigenschaften des zu bearbeitenden Materials sowie die präzise Anpassung der Zerspanungsstrategie haben einen direkten Einfluss auf die Endqualität des Bauteils, die Standzeit der Werkzeuge und die Effizienz des gesamten Zerspanungsprozesses. Was kann bei der CNC-Bearbeitung von Metallen schiefgehen – und wie lässt sich das vermeiden? Bei der CNC-Bearbeitung von Metallen können drei Hauptprobleme auftreten: 1. Vibrationen (Rattern) Sie führen zu einer unebenen Oberfläche, einer schlechteren Genauigkeit und einem schnelleren Verschleiß der Schneidflächen. Die häufigsten Ursachen sind ein zu langer Werkzeugvorschub, eine unzureichende Spannfestigkeit oder falsche Schnittparameter. 2. Falsche Schnittparameter Zu hohe Drehzahlen, zu großer Vorschub oder falsche Schnitttiefe können zu Überhitzung der Schneide, Werkzeugbruch und Verschlechterung der Oberflächenqualität führen. 3. Werkzeugverschleiß Jeder Fräser, Bohrer und Gewindebohrer hat eine begrenzte Lebensdauer – wenn er nicht regelmäßig kontrolliert wird, kann er das Werkstück beschädigen oder Fehler in der gesamten Serie verursachen. Wann lohnt es sich, die CNC-Bearbeitung von Metallen an ein erfahrenes Unternehmen zu vergeben? Bei Serienfertigung, komplexen Geometrien oder hohen Qualitätsanforderungen können durch die Zusammenarbeit mit einem erfahrenen Fertigungsunternehmen Fehler und Verzögerungen vermieden werden. Von entscheidender Bedeutung ist nicht nur ein präziser Maschinenpark, sondern auch praktische Kenntnisse über verschiedene Legierungen, deren Verhalten bei der Bearbeitung und mögliche konstruktive Einschränkungen. Zusammenfassung der CNC-Metallbearbeitung Die CNC-Metallbearbeitung ist mehr als nur das Entfernen von überschüssigem Material. Es handelt sich um einen komplexen technologischen Prozess, bei dem präzise Werkzeuge mit einer computergesteuerten Steuerung zusammenarbeiten und jeder Schritt auf Ingenieurswissen und Materialkenntnissen basiert. Dank dieser Technologie ist es möglich, komplexe Geometrien, hohe Qualität und Wiederholgenauigkeit schnell, sicher und wirtschaftlich herzustellen. Hinter einem reibungslos funktionierenden CNC-Prozess steht ein Team von Spezialisten. Der Konstrukteur erstellt ein Modell des Werkstücks, der Programmierer bereitet den Bearbeitungscode vor und der Bediener überwacht den Produktionsablauf an der Maschine. Erst die Kombination aus menschlicher Kompetenz und den Möglichkeiten moderner Werkzeugmaschinen ermöglicht eine Präzision, die mit herkömmlichen Methoden nicht zu erreichen i
Schulung zu Shrink-Fit-Technologie und Spindelklemmkraftkontrolle bei SIM Gdynia

Bei SIM Gdynia bilden wir uns ständig weiter, testen und implementieren Lösungen, die die Qualität der CNC-Bearbeitung nachhaltig verbessern. Im Mai 2025 fand in unserem Firmensitz eine technische Fachschulung statt, die von Experten der Firmen Hahn+Kolb und Diebold – führenden Anbietern von Werkzeugen und Spannsystemen – organisiert wurde. Thema des Treffens waren die Schrumpftechnik (Shrink Fit) und das Spindelklemmkraftkontrollsystem – wichtige Lösungen für Präzision, Wiederholgenauigkeit und Prozesssicherheit. Praktischer Ansatz für Innovationen An der Schulung nahmen unsere Technologen, Einrichter und Meister teil – Praktiker, die täglich für die Zuverlässigkeit der Produktion bei SIM Gdynia verantwortlich sind. Die Veranstaltung war praxisorientiert. Es wurden konkrete Fälle diskutiert, die Anwendung der Shrink-Fit-Technologie an realen Bauteilen getestet und der Einfluss der Spannkraft der Spindel auf die Stabilität und Dauerhaftigkeit der Bearbeitung analysiert. Shrink Fit ist eine Technologie zur Werkzeugbefestigung, die das Phänomen der Wärmeausdehnung nutzt – nach dem Abkühlen klemmt der Halter das Werkzeug fest und sorgt so für extreme Steifigkeit, minimale Rundlaufabweichungen und eine hohe Wiederholgenauigkeit des Prozesses. Das System zur Messung der Spindelklemmkraft ermöglicht wiederum die Kontrolle der Spannparameter in der CNC-Maschine, was sich direkt auf die Bearbeitungsqualität und die Lebensdauer sowohl der Werkzeuge als auch der Spindel selbst auswirkt. Wettbewerbsvorteile durch Wissen Wir danken den Vertretern von Hahn+Kolb und Diebold für die inspirierende Schulung und die Weitergabe ihres Fachwissens. Initiativen dieser Art sind für uns von großer Bedeutung – sie tragen zur Weiterentwicklung der Kompetenzen unseres Teams bei und wirken sich direkt auf die Produktionseffizienz aus. Bei SIM Gdynia bauen wir unseren
Was ist CNC-Bearbeitung?
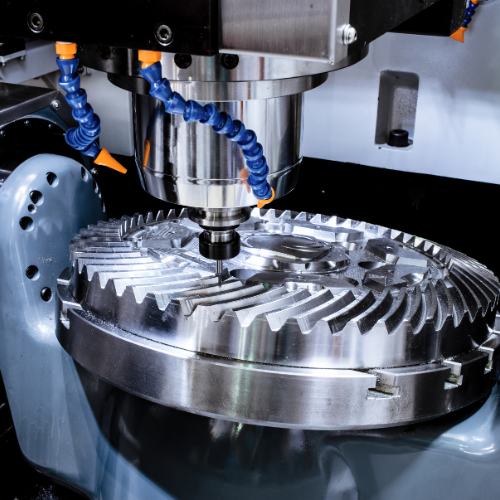
CNC-Bearbeitung (Computer Numerical Control) ist ein technologischer Prozess, bei dem Materialien mit Hilfe von numerisch gesteuerten Werkzeugmaschinen, d. h. Maschinen, die Aufgaben nach zuvor programmierten Computeranweisungen ausführen, geformt werden. Der technische Entwurf – in der Regel mit einem CAD–Programm(Computer–AidedDesign),einemWerkzeugfürdiecomputergestütztetechnischeKonstruktion, erstellt – wird in einen Code umgewandelt, der die Arbeit der Maschine steuert. CNC-Fräsmaschinen, Drehmaschinen oder Schleifmaschinen führen präzise Bewegungen aus, entfernen Material vom Werkstück und erzeugen so ein Teil mit bestimmten Formen und Abmessungen. Dies lässt sich mit dem umgekehrten Prinzip des 3D-Drucks vergleichen: Anstatt Material hinzuzufügen, wird beim CNC-Fräsen Material kontrolliert abgetragen, bis die gewünschte Form erreicht ist. Arten der spanenden Bearbeitung Es gibt mehrere Hauptarten der spanenden Bearbeitung, die jeweils unterschiedliche Ergebnisse erzielen: Die Vielfalt der Zerspanungsverfahren bietet vielfältige Möglichkeiten zur Formgebung von Bauteilen – vom groben Materialabtrag bis zur präzisen Oberflächenbearbeitung. Anwendung der Zerspanung in der Industrie Diese Technologie findet sowohl in der Serienfertigung als auch bei der Herstellung einzigartiger, spezialisierter Komponenten Anwendung. Nachfolgend stellen wir die wichtigsten Branchen vor, in denen die CNC-Bearbeitung von besonderer Bedeutung ist: Die spanende Bearbeitung spielt überall dort eine entscheidende Rolle, wo es auf Präzision, Wiederholgenauigkeit und die Möglichkeit der Bearbeitung sehr unterschiedlicher Materialien ankommt. Welche Materialien können mit CNC-Bearbeitung bearbeitet werden? Dank ihrer Vielseitigkeit kann die CNC-Bearbeitung sowohl für leicht zu bearbeitende Werkstoffe als auch für solche verwendet werden, die Spezialwerkzeuge erfordern. Zu den am häufigsten bearbeiteten Werkstoffen gehören: Die Wahl des Werkstoffs hängt immer vom Verwendungszweck des Bauteils, den Anforderungen an die Lebensdauer, die Geometrie, die Herstellungskosten und die möglichen Nachbearbeitungen ab. Vorteile der CNC-Bearbeitung Der Vorteil der CNC-Bearbeitung ist die vollständige Kontrolle über den Prozess, wodurch selbst bei sehr komplexen Projekten wiederholbare Ergebnisse erzielt werden können. Weitere wichtige Vorteile sind: Die CNC-Bearbeitung eignet sich überall dort, wo Qualität, Wiederholgenauigkeit und effizientes Produktionsmanagement gefragt sind. Zusammenfassung – Was ist CNC-Bearbeitung? CNC-Bearbeitung ist ein modernes Fertigungsverfahren, das präzise Computersteuerung mit vielfältigen technologischen Möglichkeiten verbindet. Damit lassen sich Teile unterschiedlicher Komplexität aus Metallen, Kunststoffen, Verbundwerkstoffen oder Spezialwerkstoffen effizient und wirtschaftlich herstellen. Diese Technologie findet in fast allen Bereichen der modernen Industrie Anwendung und ermöglicht sowohl die Serien- als auch die Einzelfertigung. Ihre Hauptvorteile sind Wiederholgenauigkeit, Flexibilität, verkürzte Durchlaufzeiten und geringere Materialverluste. All dies macht CNC zu einem unverzichtbaren Werkzeug für die Konstruktion und Fertigung moderner Komponenten.
SIM Gdynia unterstützt den lokalen Sport–Partnerschaft mit dem Sportverein Chwaszczyno
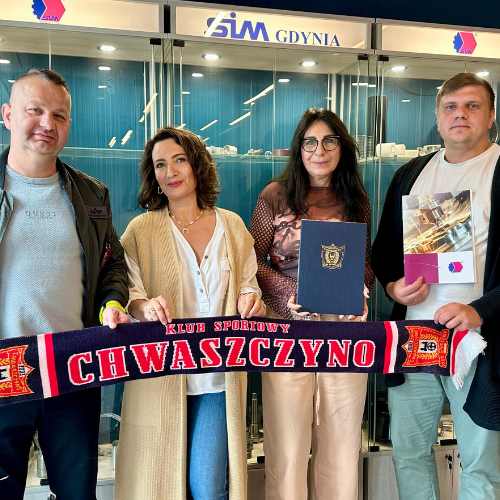
Wir bei SIM Gdynia glauben, dass die wahre Stärke der Industrie nicht nur in der Technologie liegt, sondern auch in den Menschen und Gemeinschaften, die wir unterstützen. Deshalb sind wir stolz darauf, bekannt geben zu können, dass wir am 13. Mai 2025 eine offizielle Partnerschaftsvereinbarung mit dem Sportverein Chwaszczyno unterzeichnet haben. Dies ist der Beginn einer Zusammenarbeit, die – so hoffen wir – langfristige Vorteile für junge Sportler und die lokale Gemeinschaft bringen wird. Eine gemeinsame Vision für die Entwicklung An der feierlichen Unterzeichnung der Vereinbarung nahmen die Geschäftsführerin von SIM Gdynia, Anna Szczypek, und der Vorsitzende des Sportvereins Chwaszczyno, Janusz Płocki, teil. Dieses Treffen bestätigte nicht nur die formelle Verpflichtung, sondern unterstrich auch die gemeinsamen Werte, nämlich Entwicklung, Leidenschaft und Engagement für lokale Initiativen. SIM Gdynia wurde Hauptsponsor des Vereins. Wir glauben, dass junge Sportler dank dieser Zusammenarbeit noch bessere Bedingungen für ihre Entwicklung, ihr Training und das Erreichen ihrer sportlichen Ziele – sowohl der kleinen als auch der großen – erhalten werden. Die Jugend ist die Zukunft – nicht nur im Sport Die Partnerschaft mit KS Chwaszczyno ist mehr als nur Sponsoring. Es ist eine echte Investition in junge Menschen, die dank technischer und organisatorischer Unterstützung ihre Flügel ausbreiten können. Als Produktionsunternehmen verstehen wir den Wert von systematischer Arbeit, Disziplin und Teamarbeit sehr gut – und genau das lehrt der Sport von klein auf. Mit unserer Unterstützung wollen wir die Trainingsinfrastruktur verbessern, das Trainingsprogramm weiterentwickeln und die Teilnahme an mehr Wettkämpfen ermöglichen. Wir möchten, dass jedes Kind, das beim KS Chwaszczyno trainiert, die Chance hat, seine sportlichen Träume zu verwirklichen. Wir blicken hoffnungsvoll in die Zukunft Wir hoffen, dass diese Partnerschaft der Beginn vieler gemeinsamer Projekte sein wird – Turniere, Aktionen zur Förderung der körperlichen Aktivität und Familienveranstaltungen. Unsere Unterstützung ist nicht nur ein Logo auf den Trikots – sie ist eine reale Präsenz im Leben der jungen Sportler und ihrer Familien. Wir freuen uns schon auf die ersten Erfolge der Spieler des KS Chwaszczyno, denen wir schon heute fest die Daumen drücken. Wir sind mit euch – auf dem Spielfeld und darüber hinaus!
Familienpicknick zum Kindertag – wir laden Sie herzlich ein, am 15. Juni mit uns zu feiern!
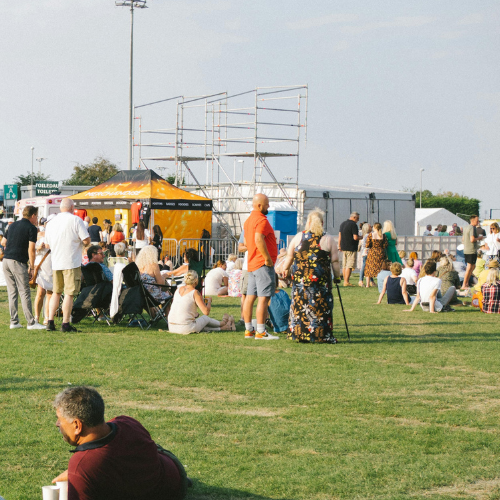
Wir bei SIM Gdynia sind davon überzeugt, dass die Stärke eines Unternehmens nicht nur auf Technologie und Präzision beruht, sondern auch auf Beziehungen – sowohl beruflicher als auch familiärer Natur. Deshalb laden wir die Mitarbeiter von SIM Gdynia und ihre Angehörigen herzlich zum Familienpicknick anlässlich des Kindertags ein, das am 15.Juni2025 im ToyotaArenaStadioninChwaszczyno stattfindet. Der Beginn der Veranstaltung ist für 13:00Uhr geplant. Warum lohnt es sich, daran teilzunehmen? Der Familienpicknick ist eine hervorragende Gelegenheit, gemeinsam Zeit in einer ungezwungenen Atmosphäre zu verbringen – fernab von den alltäglichen Pflichten, inmitten der Natur und mit zahlreichen Attraktionen für Kinder und Erwachsene. Die Veranstaltung verbindet körperliche Aktivität, pädagogische Elemente und Entspannung an der frischen Luft. All dies in einer freundlichen, sicheren und gut organisierten Umgebung. Auf dem Programm stehen unter anderem: Gewinnspiel Unter den Teilnehmern der Veranstaltung wird eine Gewinnspiel-Lotterie veranstaltet, bei der unter anderem folgende Preise zu gewinnen sind: SIM Gdynia-Zone – nur für angemeldete Mitarbeiter Für SIM Gdynia-Mitarbeiter, die sich für die Teilnahme an der Veranstaltung anmelden, haben wir einen separaten Zeltbereich mit kostenlosen Erfrischungen vorbereitet. Die Anmeldung erfolgt intern. Nur angemeldete Personen können diesen Bereich während des Picknicks nutzen. Wir sehen uns am 15. Juni in Chwaszczyno! Wir laden Sie herzlich ein, mit Ihren Familien an der Veranstaltung teilzunehmen – es erwartet Sie ein Tag voller Freude, Zusammenhalt und gemeinsamer Momente, die Ihnen lange in Erinnerung bleiben werden.
SIM Gdynia hat den OTIF95-Preis von der KION Group erhalten
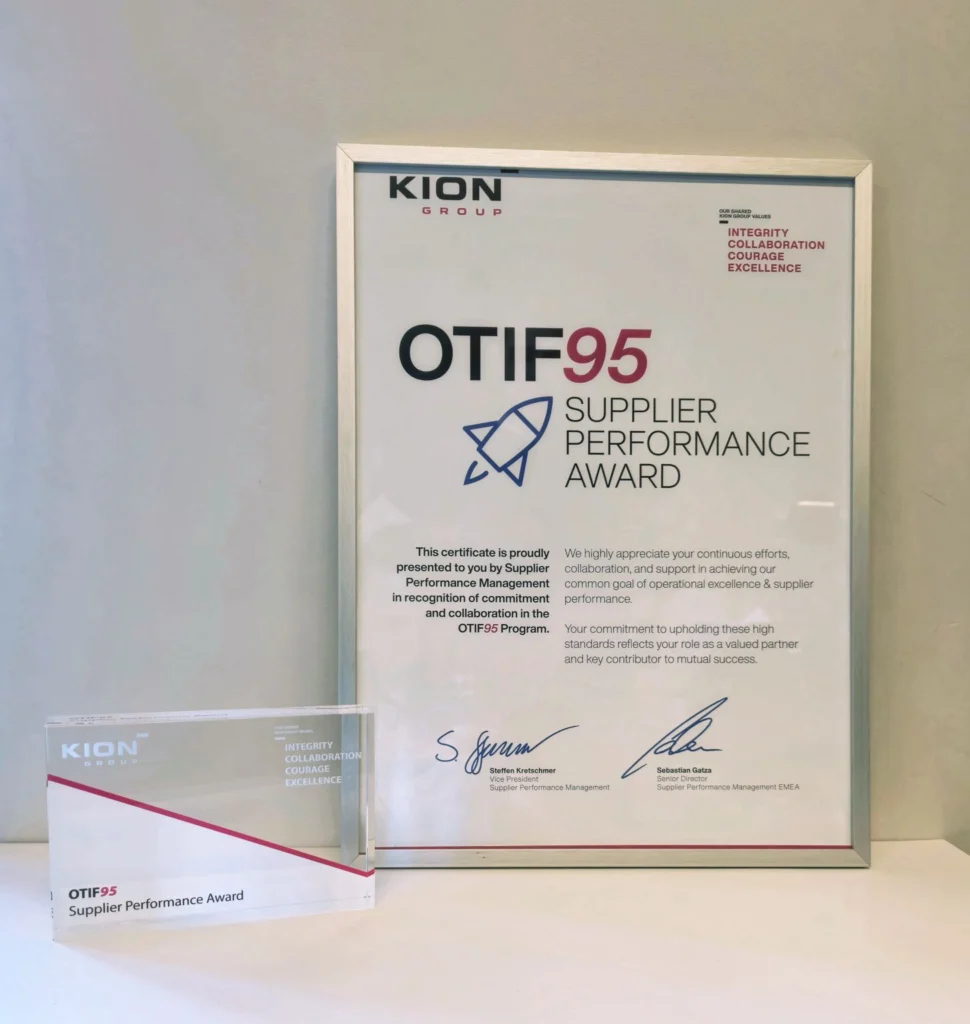
Im Februar haben wir darüber informiert, dass SIM Gdynia den OTIF95 Supplier Performance Award der KION Group gewonnen hat. Heute freuen wir uns, Ihnen mitteilen zu können, dass wir diese Auszeichnung am 03.04.2025 offiziell erhalten haben. Die Auszeichnung bestätigt unsere Zuverlässigkeit bei der Lieferung und die Effizienz unserer Betriebsprozesse. Mehr über das OTIF95-Programm und unsere Zusammenarbeit mit der KION Group erfahren Sie in unserem früheren Artikel: SIM Gdynia erhält den OTIF95 Supplier Performance Award der KION Group Wir danken der KION Group für ihr Vertrauen und ihre Anerkennung – dies ist für uns eine starke Motivation, uns weiter zu verbessern.