CNC machining of plastics – challenges and material specifics
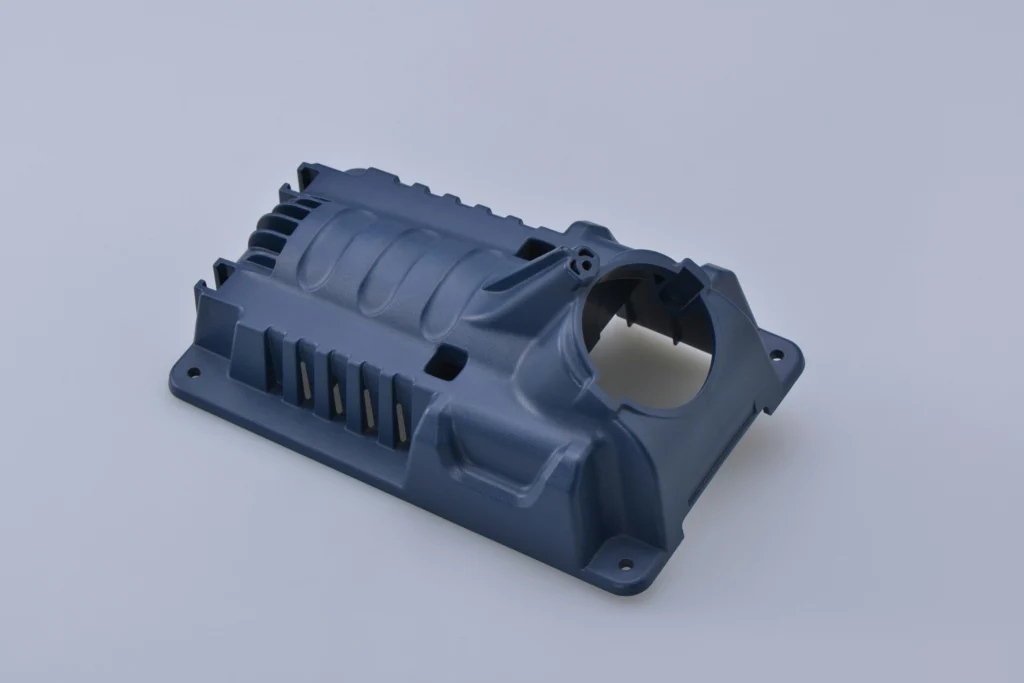
In recent decades, plastics have become a full-fledged construction material in a wide range of industries – from automotive and electronics, to medicine and more. Their growing popularity is due to a combination of low weight, chemical resistance and a wide range of mechanical properties that can be customized for a specific application. At the same time, CNC machining of plastics is significantly different from metal cutting. Polymers have completely different behavior when exposed to heat, moisture and internal stresses. This forces a different approach to design, tool selection and manufacturing strategies. In this article, we’ll take a look at the specifics of CNC machining of plastics – discussing the most common technological challenges, the differences in approach compared to metals, and the key factors that determine the quality and repeatability of production. Why is CNC machining of plastics different from metals? Plastics behave differently than metals in the machining process, mainly because of their physical and structural properties. Three factors play the biggest role here: In summary, for polymers, it is crucial to control temperature, take into account internal stresses and moisture-related dimensional stability. Properties of selected materials in CNC machining of plastics The diversity of plastics makes it difficult to speak of a one-size-fits-all machining method. Each polymer behaves differently under the influence of temperature, moisture or mechanical loads. POM (acetal) – the most predictable technical polymer POM is considered to be the easiest engineering plastic to work with. It is characterized by low moisture absorption, dimensional stability and good surface quality after cutting. Therefore, it is often the first choice for the production of precision mechanical parts requiring dimensional repeatability. PA (nylon) – a material that requires moisture control Nylon is distinguished by its high mechanical strength, but its disadvantage is its strong hygroscopicity. Absorbed water changes not only the dimensions, but also the hardness and elasticity of the material. For this reason, many mills use drying of semi-finished products before machining, as well as stress-relief annealing before cutting. (A heat treatment process that involves heating the material, holding it at a given temperature and slowly cooling it to remove internal stresses) PC (polycarbonate) – strong, but prone to stress cracking Polycarbonate is prized for its exceptional impact resistance. Unfortunately, at the same time it is prone to micro-cracking under internal stresses and in contact with certain coolants and solvents. To reduce the risk, sharp tools, cooling with neutral media and an annealing process at critical parts are used. PMMA (acrylic) – a material for optical applications Acrylic is the material of choice where transparency and high surface aesthetics are required. However, annealing both before and after processing is necessary to achieve dimensional stability. In optical applications, flame or chemical polishing is additionally used to remove microcracks and improve transparency. PTFE (Teflon) – a material flow problem PTFE is a polymer with a very low coefficient of friction and excellent chemical resistance. Its disadvantages are softness and a tendency to so-called creep – that is, slow deformation under load. CNC machining here requires particularly rigid fixtures and sharp tool geometry. PEEK – a high-performance polymer PEEK is one of the most expensive and advanced engineering polymers. It exhibits high thermal and mechanical resistance. Its CNC machining is relatively predictable, provided the material has been annealed beforehand. For glass or carbon fiber reinforced composites, PCD or diamond tools are recommended. Dimensional stability and tolerances in CNC machining of plastics One of the key issues in CNC machining of plastics is the dimensional stability of the parts. It depends not only on the accuracy of the machine tool, but also on the history of the material. In our experience, tolerances of ±0.0005 inches can be achieved under favorable conditions, but only for stable materials (e.g., POM, PEEK) and with proper environmental control. The importance of designing under plastics Designing plastic parts requires a different approach than for metals. Polymers are more susceptible to stress concentration, deformation or closing of holes after machining. Therefore, the properties of the material must be taken into account already at the design stage. In practice, this means, among other things, avoiding sharp internal angles (which initiate cracks), using radii at corners, selecting appropriate wall thicknesses and preferring threaded inserts to threads made directly into the plastic mass. Summary CNC machining of plastics is an area that requires experience and an understanding of material specifics. Unlike metals, where heat and stresses are easier to control, polymers require a customized approach. With knowledge of these relationships, it is possible to achieve high surface quality and stable dimensions, making plastics a full-fledged material in modern industry.
CNC machining of brass – properties, grades and best practices
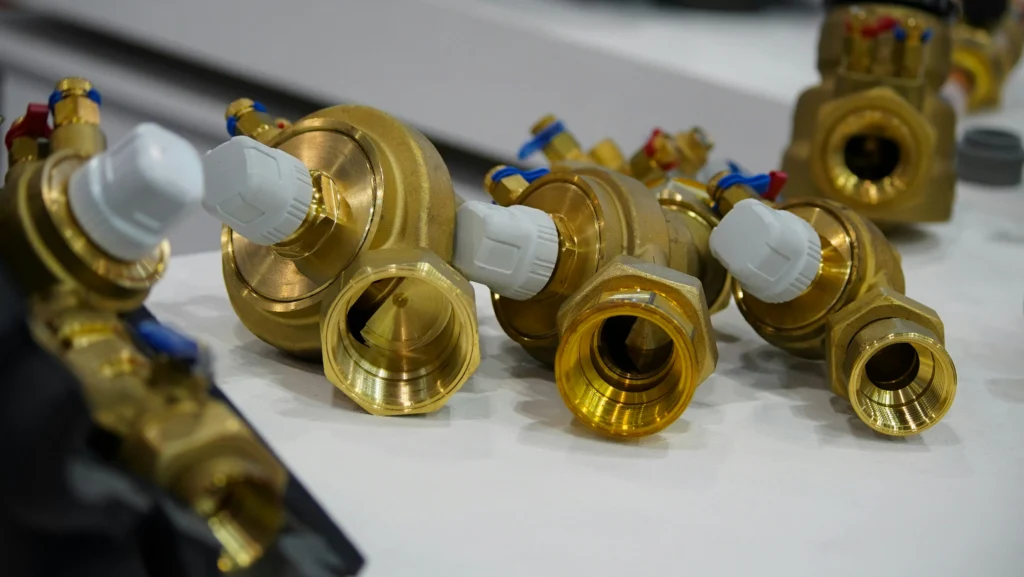
Brass, an alloy of copper and zinc, is one of the most commonly chosen nonferrous metals in CNC machining. It is valued for its ease of machining, corrosion resistance and attractive surface appearance. Thanks to these properties, it is used in fittings, electrical parts, precision components or decorative details. The importance of brass in industrial production is due not only to its functional properties, but also to the economy of the process – in many cases, it makes it possible to achieve high quality parts with relatively short processing times. In this article, we will introduce the properties of brass relevant to CNC machining, discuss the most common grades of this alloy, and suggest, based on our more than 45 years of experience, how to approach turning, milling, drilling or tapping for optimal results. Brass and CNC machining In metal CNC machining, brass stands out from many others. Its thermal conductivity reduces the risk of tool overheating, and its relatively low hardness makes for a smooth process. This makes it possible to use high cutting speeds and achieve very smooth surfaces without additional polishing. It is these features that make CNC turning and milling of brass one of the particularly cost-effective processes. Appropriately selected cutting parameters allow rapid removal of excess material while maintaining high surface quality. The most common grades of brass Several key varieties of brass are encountered in industrial practice: Knowing these differences can help you avoid mistakes and optimize your cutting process. CNC turning and milling of brass – what is worth knowing? Turning brass is one of the basic operations in CNC machining of this alloy. In order for the process to be stable and give high surface quality, it is used: Brass milling is also one of the very efficient processes, provided the right choice of tools is made: Drilling and tapping brass Drilling in brass has a peculiar difficulty – in some grades, especially soft and ductile ones, there is a phenomenon colloquially called “drill retraction”. This means that instead of stable cutting, the tool is sucked deep into the material, leading to too rapid deepening of the hole, loss of control over the process and even breaking the drill bit. To prevent this, drills with modified geometries – with zero or slightly negative rake angle edges – are used. This ensures that the tool actually cuts the material, rather than “pulling” deep into the hole. The result is a stable process and better hole quality. Brass threading goes smoothly, as long as the tools are well matched to the type of hole and alloy: Cooling and lubrication during CNC machining of brass For lead grades, dry machining or machining with minimum lubrication (MQL) is possible. Due to short chips and high thermal conductivity, excessive tool heating does not occur. The situation is different for lead-free alloys, which have poorer thermal conductivity. In their machining, it is crucial to use emulsion or oil cooling, which significantly extends tool life and improves surface quality. Health and safety aspects in brass machining For lead grades such as CW614N, it is important to be aware of health hazards. While the lead present in the alloy improves machinability, it is also a toxic agent. Dust and fine particles generated during machining can be inhaled or transferred to the body through hand contact. Prolonged exposure to lead is associated with the risk of nervous system disorders, circulatory problems or kidney damage. Therefore, brass processing plants should use: In the case of lead-free brasses, this risk is virtually eliminated. Summary CNC machining of brass is one of the efficient and relatively easy processes, but each grade of material requires an individual approach. Leaded brasses provide exceptional machinability, while lead-free grades require parameter modification and cooling, but are environmentally and health safer. Choosing the right tools, cutting parameters and cooling system produces precision parts with high surface quality, making brass one of the key materials in modern industrial manufacturing.
New investment in SIM Gdynia machine park – laser marking machine HBS-GQ-20F
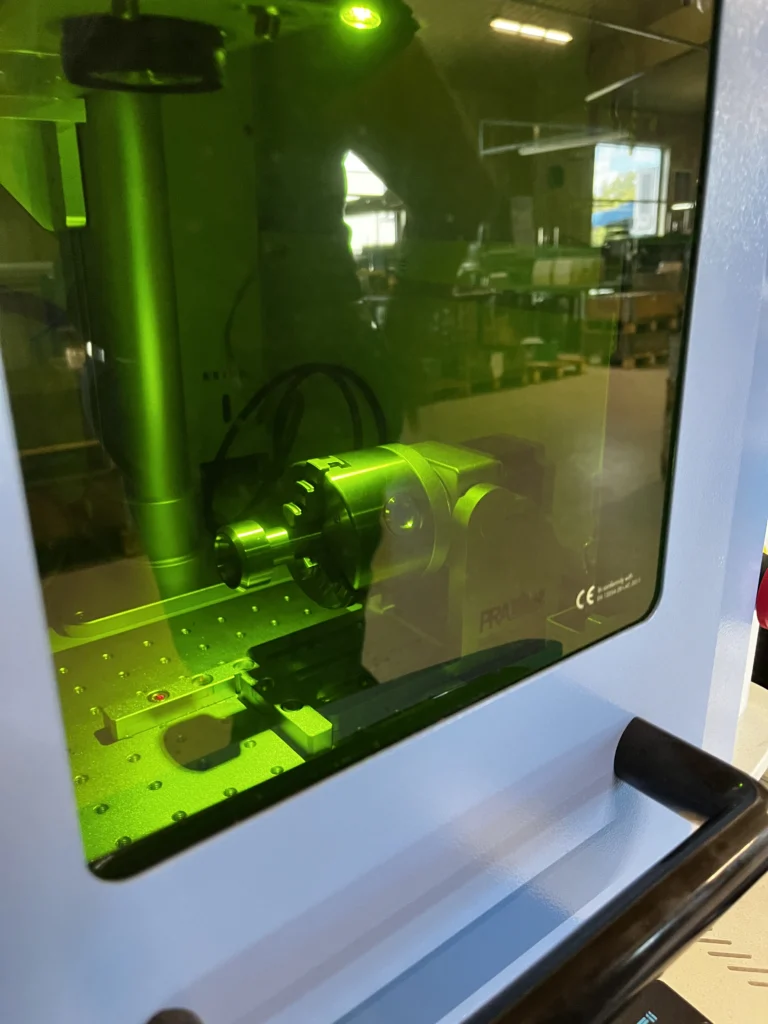
Following the spirit of time and responding to the growing demands of the market at SIM Gdynia, we invested in a modern laser marking machine HBS-GQ-20F. This device, equipped with a Windows-based system, significantly speeds up the process of configuration and setting of working parameters, which directly translates into shorter marking time – especially in the case of large series of parts. Why HBS-GQ-20F? The HBS-GQ-20F laser marking machine is distinguished by its Enclosed Marking Station design – an enclosed working chamber that increases operator safety and facilitates the handling of complex parts. Thanks to the spacious design, it is possible to place workpieces with unusual shapes without problems and use additional marking accessories. As the manufacturer emphasizes, the GQ-20F model is a “mega body, mega capability” – a device created for intensive industrial use, which works well in both marking small components and larger parts requiring precise engraving. Key technical parameters The new machine gives us the ability to mark in various configurations, offering, among other things: The machine is air-cooled, which facilitates operation and reduces maintenance costs. Works with popular graphic file formats (.ai, .plt, .dxf, .tiff, .jpg), which gives great flexibility in project preparation. Optional lenses – different marking fields Depending on your needs, the HBS-GQ-20F can be equipped with lenses that allow you to work with marking fields: This makes it possible to mark both very small and large components, further increasing the versatility of the system. Benefits for SIM Gdynia customers The purchase of a new laser marking machine is another step in the development of our machine park. With the HBS-GQ-20F, we can provide: The new technology allows us to better meet the needs of customers in a variety of industries – from engineering to energy to the medical and defense sectors.
SIM Gdynia at MSPO 2025 – with a new concession and new opportunities
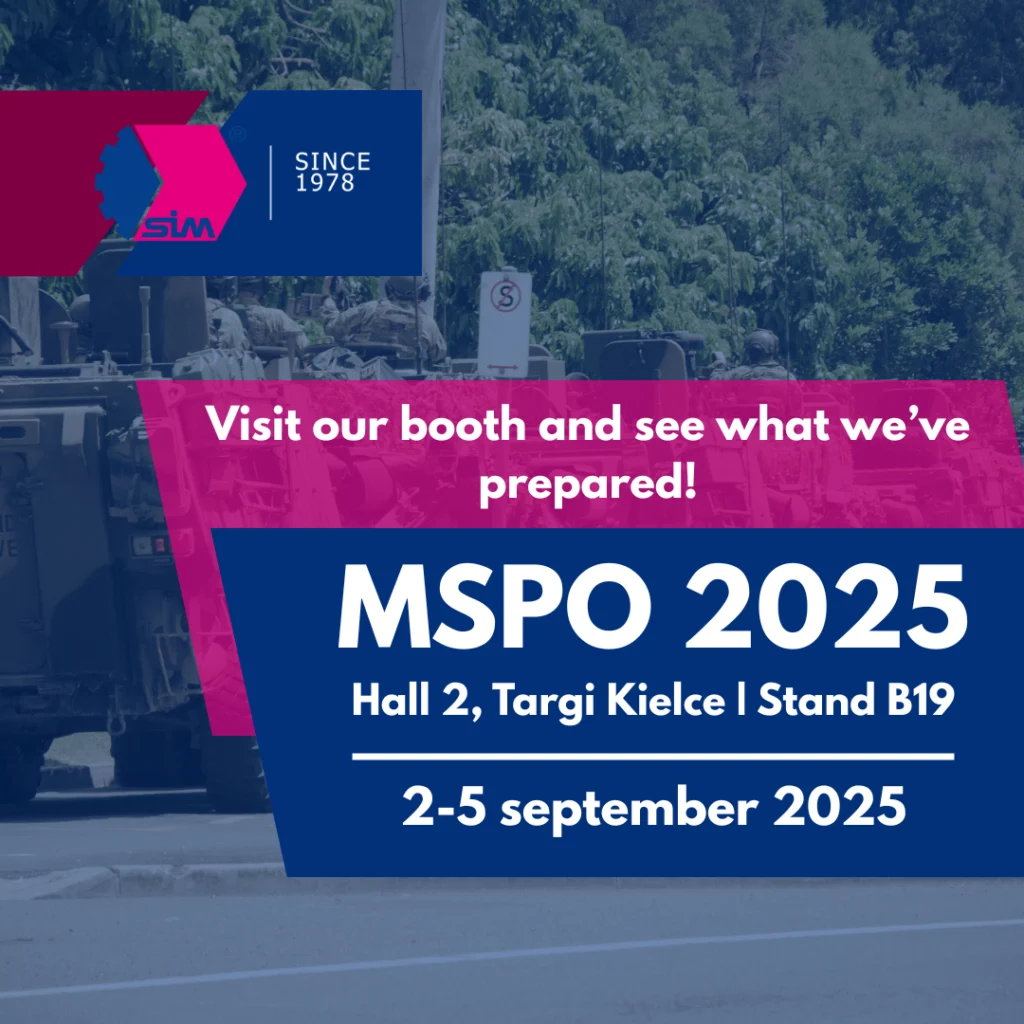
The MSPO Fair is the largest defense industry event in Central and Eastern Europe, bringing together the most important manufacturers, technology suppliers and decision-makers from around the world every year. It is a space where the military meets industry, and innovative technological solutions become the answer to the growing needs of security and modern defense. This year, we will again participate in the International Defense Industry Exhibition as an exhibitor, presenting our latest competencies, CNC machining technologies and new opportunities resulting from the concession we have obtained for projects for the military sector. MSPO – a meeting place for industry, technology and security Organized by Targi Kielce, the event has for more than 30 years played a key role in shaping relations between suppliers of solutions for the military and procurers – both domestic and international. Previous editions have been attended by more than 600 companies from dozens of countries, and the fair halls have been visited by thousands of specialists, engineers, military delegations and government officials. MSPO is not only an exhibition of equipment and technology, but also an opportunity to establish concrete business contacts, talk about projects and present their own capabilities in the context of the real needs of the defense sector. SIM Gdynia – CNC for defense Our presence at MSPO 2025 has a special character. In July of this year, we received an official license to carry out projects for the defense sector, which formally confirms our readiness to produce components that meet the highest requirements in terms of quality, safety and compliance with standards. During the fair, we will present our core competencies in: Precision CNC machining of metal and plastic components, implementation of complex mechanical designs for military applications, working with difficult materials and large-size components, quality control and finishing processes that meet industry standards. Where to find us during MSPO 2025 You are cordially invited to visit our booth: Hall 2, Booth B19 September 2-5, 2025 | Kielce Trade Fair Our team will be available to present SIM Gdynia’s offer and talk about cooperation opportunities in the area of military and defense projects. We invite you to talk about projects with a future SIM Gdynia is a partner for those looking for a proven contractor with experience, flexibility and access to advanced CNC technology. Our participation in MSPO 2025 is not only a presentation of our offer – it is also an open invitation to dialogue, exchange knowledge and plan future-oriented projects. If you are interested in cooperation in the field of precision machining of components for military applications, we encourage you to contact us or meet directly during the fair. See you in Kielce.
SIM Gdynia has obtained a license for the production of weapons and military technology
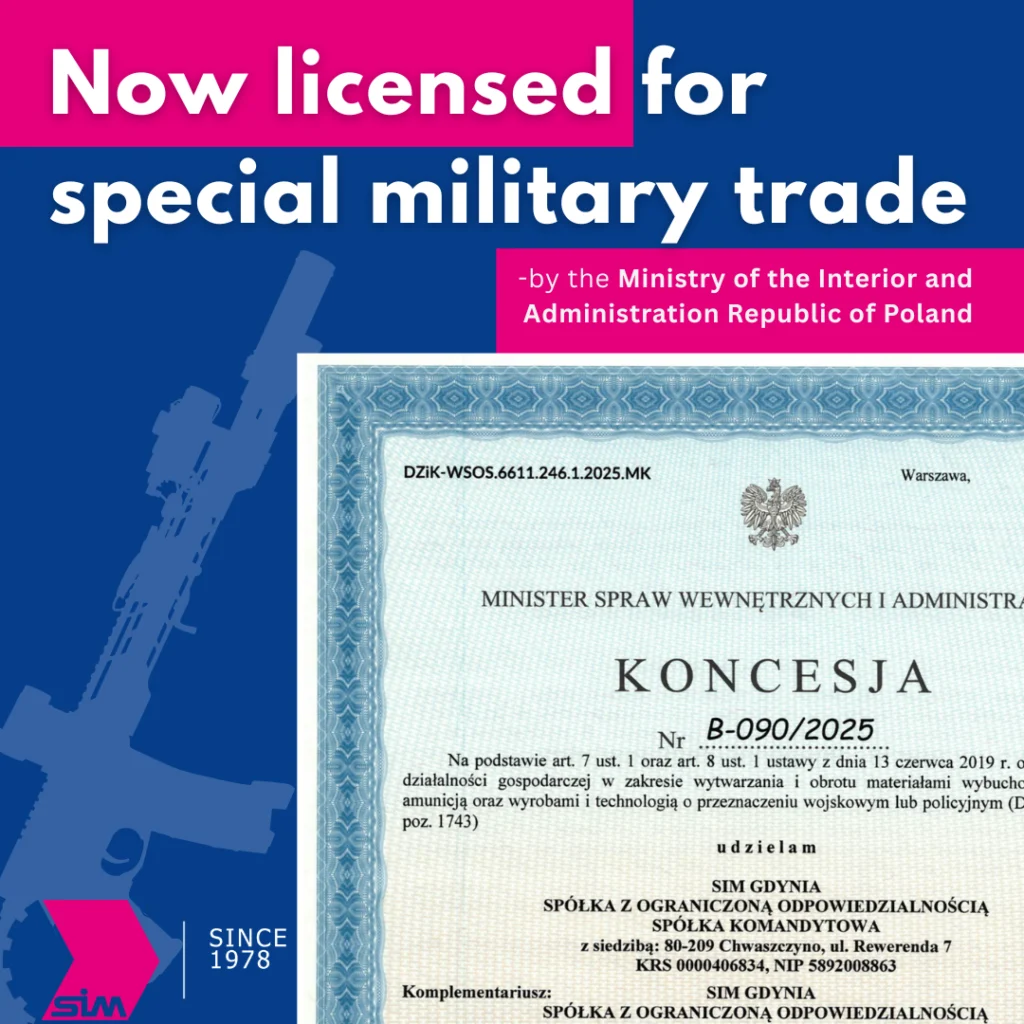
We are proud to announce that on July 4, 2025, SIM Gdynia Sp. z o.o. Sp.k. obtained a license from the Ministry of Internal Affairs and Administration (No. B-090/2025) to conduct business activities in the field of manufacturing and trading in weapons, ammunition, explosives, as well as technologies for military or police use. This is a breakthrough moment in our history, confirming that SIM Gdynia is not only an experienced manufacturer of mechanical components, but also a reliable and fully authorized partner for state institutions and entities operating in the field of security and defense. Confirmation of our competence Obtaining a license from the Ministry of Internal Affairs and Administration is not just a formality – it is the result of a meticulous verification of our processes, resources, and compliance with safety and state supervision regulations. Receiving this document confirms the highest operational standards and full transparency of our activities. For our current and future customers, this is a clear signal: SIM Gdynia is a partner ready to implement projects of strategic importance – from individual components to complex mechanical systems for the defense sector. Ready for new challenges Thanks to our extensive machine park, experience in advanced CNC machining, and our own research and quality control department, we can fulfill orders that require the highest precision, confidentiality, and compliance with restrictive technical standards. We have the technological facilities necessary to produce both short prototype series and full production batches dedicated to military and police applications. We invite you to cooperate with us We are ready to support projects that require special expertise and authorization. If your company is looking for a proven manufacturer of special-purpose components, please contact us. We will be happy to discuss the possibilities of cooperation and tailor our offer to the individual needs of your project.
Surface finishing after CNC machining – what you need to know about the final stage of machining
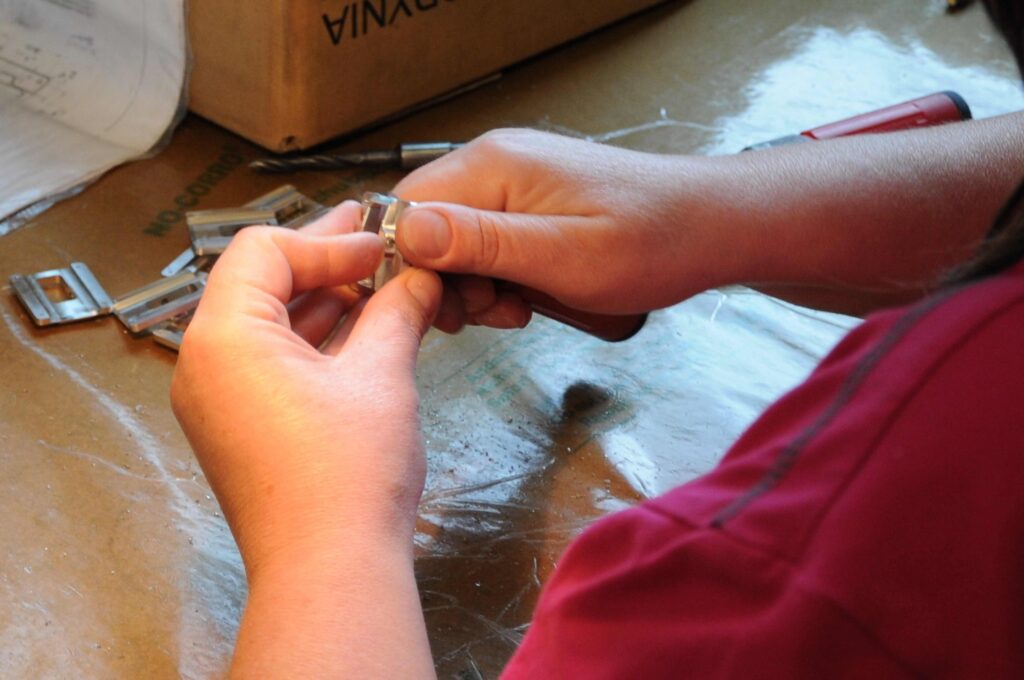
CNC machining is a process that allows you to obtain a precise shape and the required dimensional tolerance for a component. However, the component obtained is not always ready for use immediately after milling or turning. The surface finishing process is crucial for the final quality and functionality of the part. This is when the machined surface is smoothed, cleaned, and adapted to the target operating conditions. Choosing the right finishing method can determine the durability, resistance, and aesthetics of a component. Even minimal burrs, unevenness, or tool marks can affect the performance of technical systems, leading to leaks, accelerated wear, and even damage. Why is surface finishing after CNC machining so important? Proper surface finishing has a direct impact on the functional parameters of CNC-machined parts. Among other things, it: A well-executed finishing stage significantly increases the utility value of the component and prevents costly failures during operation. Overview of finishing methods Depending on technical, aesthetic, and functional requirements, CNC-machined components are subjected to various finishing methods. Each of them has a specific application and affects the final surface quality. Deburring Deburring is the process of removing burrs and sharp edges. It can be done manually (e.g., with knives, files), mechanically (with brushes, cutters), or thermally. It ensures safe and clean surfaces of parts, ready for further processing. Tumbling In this method, parts are placed in a drum with abrasive materials and liquid. The rotation of the part causes gentle smoothing, thus eliminating surface roughness, which is ideal for mass production. The process improves appearance and removes microscopic imperfections. Precision grinding This is a mechanical method that achieves very low roughness (Ra < 0.4 µm). Ideal for components requiring high tightness, fit, and precision. Used, for example, in hydraulic components. Polishing This involves smoothing the surface with polishing pastes and tools. It improves aesthetics and reduces dirt adhesion. Protective coatings How to choose the right finishing method? The choice of the right finishing method depends on several key factors: For stainless steel, deburring is most commonly used due to the need to remove burrs. For aluminum, anodizing is the most popular choice, as it creates a hard and corrosion-resistant protective layer while enhancing the aesthetic qualities of the part. Machine housings, on the other hand, are usually subjected to deburring, shot peening and galvanizing. Here, not only aesthetics are important, but above all user safety and effective corrosion protection, especially in humid or chemically aggressive environments. Summary Surface finishing is not an addition, but an element of the standard CNC machining process. It directly affects the quality, repeatability, and durability of the part. In industrial practice, finishing is treated as a critical element—one that determines the reliability of the finished component and its resistance to operating conditions. Therefore, the choice of the appropriate method should be planned at the technological design stage.
CNC steel machining – how to machine the most popular material in manufacturing?
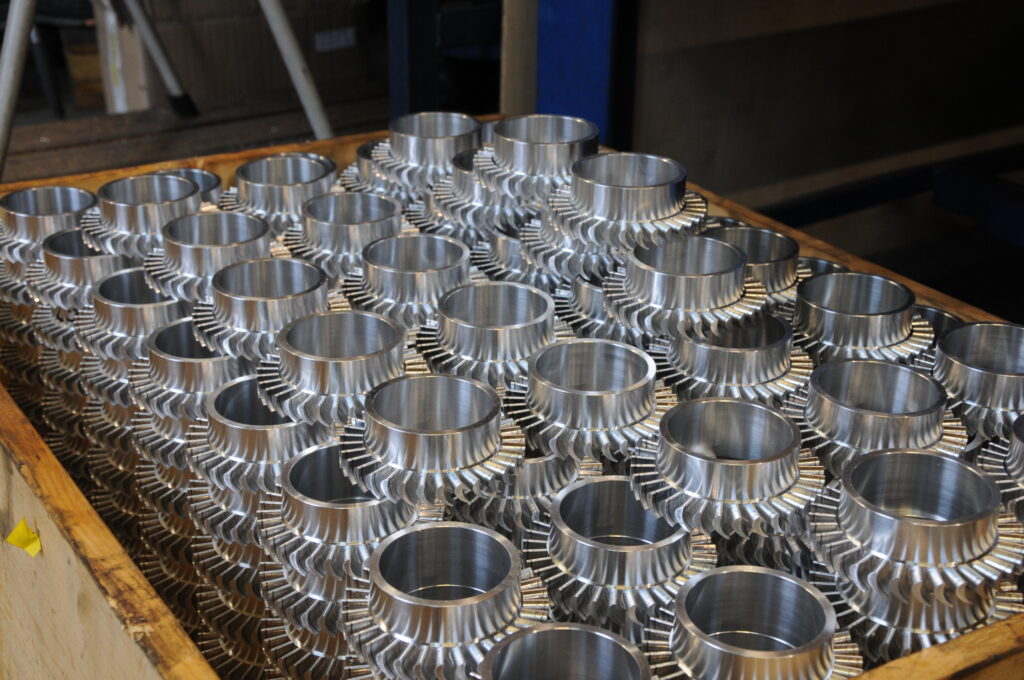
In the manufacturing industry, steel is one of the most important structural materials. Its popularity stems from its wide availability, a broad range of mechanical properties, and the possibility of modifying its structure through alloying and heat treatment. In practice, this means that two seemingly similar grades of steel can react completely differently to cutting and turning. In this article, we look at the properties of steel that determine its behavior in CNC metalworking. We show why knowledge of the material grade is not a formality, but the foundation of a well-planned technological process. Characteristics of steel and its applications in modern CNC machining Steel is an alloy of iron and carbon. It may contain alloying additives such as chromium, nickel, molybdenum, or manganese. These components allow for different physical and chemical properties of the material. The most commonly used alloying additives for steel are: The most common types of steel: Knowledge of the properties of a given steel grade is crucial when planning CNC machining. It determines which tools, parameters, and coolant should be used. Steel grades and CNC machining – how do they affect the selection of technological parameters? The properties of the material determine how it will behave in contact with the tool and what technological conditions should be adopted to achieve a stable, repeatable process. Low-carbon steels They are characterized by good plasticity and ease of machining, but lower strength. They can be machined at higher feed rates with less risk of tool damage. High-carbon steels Significantly harder and more resistant to abrasion, but more difficult to machine. They require sharp tool geometry and reduced cutting speeds to avoid overheating and vibration. Alloy steels (e.g. with added chromium, nickel, molybdenum) They are characterized by increased strength, corrosion or wear resistance. They require an individual technological approach – both in the selection of coolant and cutting strategy. Stainless steels Difficult to machine due to their tendency to form build-up on the cutting edge. High chromium and nickel content increases corrosion resistance but also impairs machinability. Very sharp tools and intensive cooling are required. Tool steels Heat-treated to achieve high hardness. They require tools with high wear resistance. The presence of molybdenum and vanadium improves resistance to overheating and abrasion during intensive cutting. Tools and machines for CNC machining of steel In modern CNC machining of steel, a wide range of specialized tools and machines are used, adapted to the type of material being machined and the machining method: It is important to select the right machining parameters, such as cutting speed, feed rate, and cutting depth, for the properties of the material. Typical errors during CNC machining of steel and how to eliminate them Steel in a machining environment requires constant monitoring of parameters and adaptation of tools to the type of material. The most common problems include: To minimize the risk of errors, it is worth implementing test runs, using cooling adapted to the steel grade, and monitoring the process with vibration and temperature sensors. Summary – what to remember about CNC machining of steel CNC machining of steel is a complex but fundamental process in modern industrial production. In order to achieve high quality and repeatability of parts, it is necessary to understand the properties of a particular steel grade and to adapt the appropriate tools, cutting strategies, and machine tool operating parameters to them. The precise selection of tools (cutters, inserts, drills), effective cooling, and the rigidity of CNC machines are of key importance here. Avoiding common mistakes such as overheating tools, poor clamping, or overly aggressive cutting translates into longer tool life and optimization of the entire process. The right approach to steel machining is not only a matter of technique, but also of efficiency, quality, and reliability.
The latest investment in the HBS‑GQ‑20F laser marking machine – even greater possibilities at SIM Gdynia
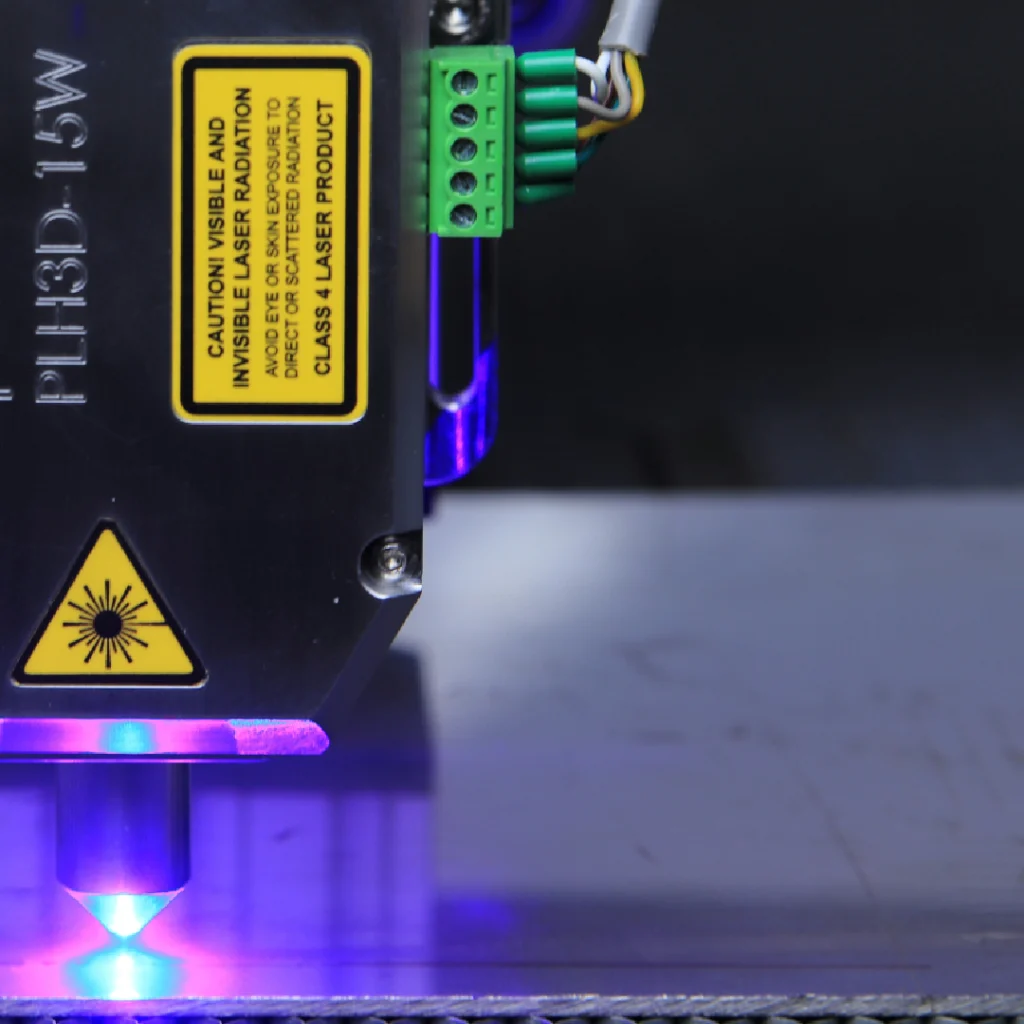
At SIM Gdynia, we are constantly investing in technologies that increase the precision, efficiency, and quality of our services. The latest step in this direction is the purchase of a modern HBS‑GQ‑20F laser marking machine. This device allows us to mark large series of parts even more efficiently, with greater accuracy and in less time. A new quality of marking at SIM Gdynia The HBS‑GQ‑20F laser marking machine is a modern solution dedicated to the precise marking of metals and plastics. Thanks to its closed design, high safety class and advanced automation, this device perfectly fits our production needs. The integrated Windows operating system allows for quick and intuitive process configuration, which significantly speeds up production preparation, especially for large volumes. Key technical data of the HBS-GQ-20F Parameter Value Marking area 110 × 110 mm (optional: 65 × 65 mm, 170 × 170 mm, 220 × 220 mm, 300 × 300 mm) – depending on the lens used Marking depth Up to 1.2 mm – adjustable depending on the material and number of passes Marking speed Up to 12,000 mm/s – very fast marking with high quality Positioning accuracy ± 0.001 mm – extremely precise reproduction in the same place even with large series Laser power 20 W, 30 W, 50 W or 100 W – depending on requirements, from delicate marking to engraving hard materials Laser source operating time Up to 100,000 hours – long service life without frequent replacement of components Power supply/energy consumption 220 V / max. 500 W – low operating costs, connection to a standard industrial socket Cooling Air-cooled – no water or additional cooling systems required Operating conditions Temperature from –10 °C to +60 °C, humidity 5–95% – stable operation even in harsh production environments Supported file formats AI, PLT, DXF, TIFF, JPG and others – compatibility with popular graphics and CAD software A new standard at SIM Gdynia Thanks to this investment, we can mark mechanical components faster, more precisely and more efficiently than ever before. This means benefits for both us and our customers.
Report from the ITM INDUSTRY EUROPE 2025 trade fair – SIM Gdynia at the center of industrial innovation
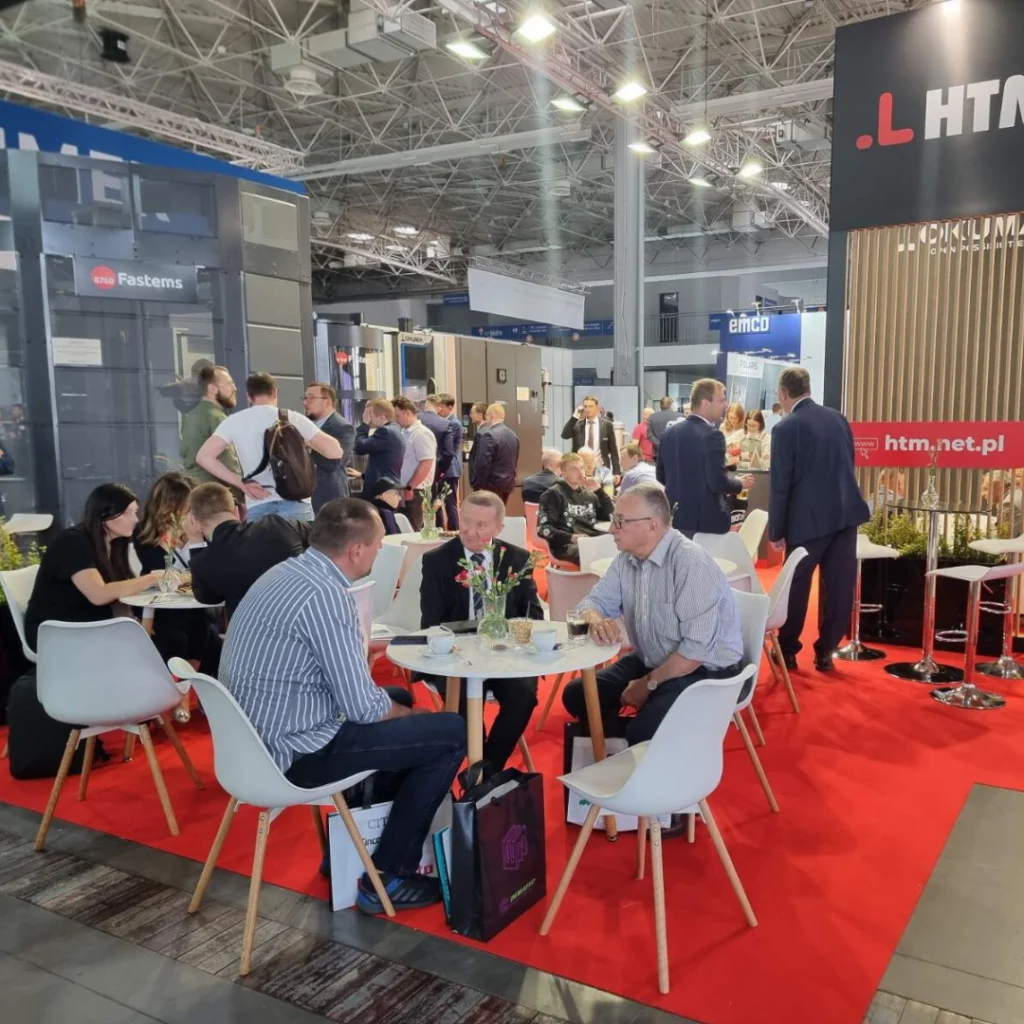
On June 4, 2025, three representatives of our staff took part in the ITM INDUSTRY EUROPE trade fair in Poznań. This event attracts leading representatives of European industry every year, offering a space for knowledge exchange, trend observation, and strategic purchasing decisions. What is ITM INDUSTRY EUROPE? ITM INDUSTRY EUROPE is the largest and most comprehensive industrial event in Central and Eastern Europe. It takes place in Poznań and attracts thousands of professionals from industries related to metalworking, automation, robotics, metrology, and future technologies. Under the common banner of ITM, machine manufacturers, system integrators, engineers, and leaders in digital solutions for industry come together. The main idea of the event focuses on Industry 4.0 – the full integration of production processes with digital analytics, automation, and artificial intelligence. Investments and inspiration During our presence at ITM INDUSTRY EUROPE 2025, we had the opportunity to analyze a number of modern solutions, compare technologies, and hold many valuable discussions with suppliers of production support systems. We are returning from this visit not only with new knowledge, but also with concrete decisions. We have made an investment that will translate into further improvements in our technological and operational processes in the coming months. This is a strategic step for us towards increasing efficiency and maintaining the highest quality standards we offer our customers. Summary Participation in ITM 2025 confirmed that the future of industry belongs to companies that can combine precision, automation, and digitization. Thanks to our presence in Poznań, we better understand the market development trends and the needs of our partners. We would like to thank the event organizers for creating a space that truly supports the development of industry in Poland and Europe.
Investing in your own machine park or CNC outsourcing?
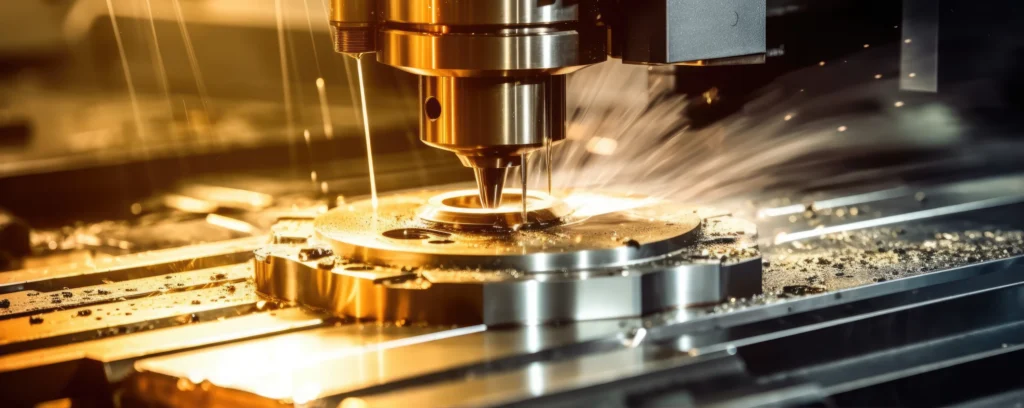
The decision of whether to build your own CNC machine park or use the services of a subcontractor who will manufacture mechanical components on request is one of the most important operational choices in the industrial sector. It is a choice that affects not only the company’s finances, but also the time needed to implement new products, the availability of technology, operational flexibility, and design risk. Not every manufacturing company needs to invest millions of dollars in modern machining centers and build technological facilities from scratch. On the other hand, it is not always worthwhile to outsource processes that are critical to quality, confidentiality, and precision. In this article, we will analyze both approaches: investing in machines and outsourcing CNC machining, based on specific figures, real scenarios, and proven market practices. The costs of investing in a CNC machine park – what do you really need to consider? Buying a machine is just the beginning. Your own CNC machine park generates a number of additional costs that must be taken into account at the investment planning stage: It is worth noting that CAM systems can be offered as perpetual licenses with an annual fee for updates or in a subscription model, where you pay annually. Price differences result from functionality, the number of machine axes, access to simulation and post-processors. For an example 5-axis center, annual operating costs – excluding depreciation – can easily exceed PLN 400,000. This is a real challenge, especially if the machine is not working at full capacity. Source: want.net – CNC Machine Cost Explained Is 2,000 hours the break-even point? In an industrial environment, it is generally accepted that approximately 2,000 machine hours per year is the approximate break-even point for an investment in a CNC machine tool. Where does this figure come from? It is roughly equivalent to the full utilization of a single machine in a single-shift system: 8 hours per day, 5 days per week, 50 weeks per year (with a reserve for service downtime and holidays). Above this threshold, the investment begins to pay for itself – unit production costs decrease and capital efficiency increases. The longer the machine runs, the better the ROI (Return on Investment). But in practice, this threshold can be difficult to achieve. Market data shows that the average utilization of CNC machines in single-shift plants is only 26% of available production time – significantly less than the required 2,000 hours. This is the result of underutilization, downtime, changeovers, and variable orders. Conclusion? 2,000 hours is a realistic but ambitious goal that only pays off with regular, well-planned production volumes. In other cases, outsourcing should be considered as a solution with lower financial risk. Source: https://www.machinemetrics.com/stateoftheindustry2022 When is it worth investing in your own CNC machine park? Having your own CNC machine park is a solution that can bring tangible benefits. This is especially true when: While some of these needs can be met by external contractors, having your own machines gives your company decision-making independence, shorter response times, and the potential to optimize technology in real time. What does CNC machining outsourcing offer? Outsourcing in the production of mechanical components is now much more than just ordering a part. Modern service companies are becoming technology partners, offering access to specialized machines without the need to build infrastructure from scratch. Within a single partnership, you can obtain: Importantly, outsourcing also gives you access to the experience of a team that has been implementing projects for many industries for years. This experience translates into better technological advice, faster implementation, and a lower risk of errors during production. When is outsourcing CNC machining advantageous? Outsourcing CNC machining is worth considering when: More and more companies are using a mixed model – keeping basic production in-house and outsourcing more complex or occasional orders to external partners. Summary The decision on whether to develop your own machine park or outsource CNC machining is not just a matter of calculating the unit cost of production. It is a strategic choice that affects your operating model, cost structure, and project delivery speed. Investing in machines is a good idea when you have a large, stable volume, need full control over the process, and have clearly defined technical competencies within the company. It’s a model that gives you independence, but it requires capital, planning, and high machine utilization to be profitable. Outsourcing CNC machining, on the other hand, is a flexible, scalable and low-risk solution. It works well for companies that operate with variable demand, develop new products or need quick access to technology that is not cost-effective to implement permanently.